Improved Paint Bonding, Optimized Processing of Painted Components: Boosting Adhesion with Plasma Technology
Industrial companies face unique challenges posed by surfaces that are coated with paint and then processed. The automobile industry is a good example. Metal or plastic components are bonded as part of the production process, and plasma technology can help here.
The Plasmatreat GmbH, based in Steinhagen, shows how plasma can create long-lasting adhesive bonds and discusses the additional benefits and opportunities that plasma can offer. The company specializes in the development, manufacturing, and use of atmospheric plasma technology in industrial production.
Surfaces can be painted for decorative purposes, but painting also has a protective function. The paint makes the product look attractive, and it also reliably protects the
substrate from environmental factors such as moisture, dirt, UV light, and more.
However, when it comes to painted surfaces the industry often faces various challenges. The challenges arise when the paint is decorative and protective but doesn’t adhere to the surface properly, or when a painted surface has to undergo further processing – such as when a painted component needs to be bonded.
And it’s in precisely these problem areas where plasma technology can be particularly helpful during the production process.
Plasma Technology and What It Exactly Can Do
Plasma pretreatment is the key technology for microfine cleaning, surface activation, and plasma coating of practically any material. It is based on a simple physical principle:
Adding energy causes matter to change its state.
If energy is added to a gas, it ionizes and becomes energized plasma, the fourth state of matter. If the plasma, with its high energy level, then comes into contact with materials,
the surface properties of those materials change – as when a hydrophobic surface becomes hydrophilic, for example.
This means plasma can be used to alter the surfaces of substrates in a targeted way. Plasmatreat specializes in surface treatments with atmospheric pressure plasma and offers a myriad of processes for a wide range of different applications.
Microfine cleaning with Openair-Plasma safely and gently removes dust, grease, release agents, and additives from surfaces. Additionally, incorporating groupings containing oxygen and nitrogen into mostly non-polar materials, for example, results in increased surface energy and is known as activation.
This optimizes the wettability of the surface, allowing for a significant increase in the surface’s adhesive properties. This enables long-term stable adhesion - of paint to surfaces such as plastic or metal, for example.
The PlasmaPlus process creates nanolayers, resulting in functional surfaces with defined properties. Specific additives are added to the plasma for various applications via jet heads developed especially for PlasmaPlus applications. The plasma excites the additives, significantly increasing their reactivity.
This allows the substances to optimally attach to the material surface during the plasma coating process and to bind to it firmly.
The result is a nanolayer with functional surface properties that can be individually tailored to the process, such as an anti-corrosion coating or a layer of bonding agent that is applied inline during production and can be processed further directly after application.
Fields of Application: Adhesion Improvement and Bonding
We use plasma technology to improve the adhesion between the paint and the substrate, for one. Treating the surface with Openair-Plasma, allows that paints will achieve a level of adhesion to the substrate that would not otherwise be possible.
The products used in industrial applications offer varying levels of adhesion on different surfaces such as plastic or metal. Special additives are added to the paints to lend them additional properties, such as resistance to dirt, moisture, or sunlight.
But these additives often impact the adhesion: The paints no longer form an optimal
bond with the substrate. In order to avoid compromising on functionality, industrial companies use a range of different pretreatments, such as sanding, sandblasting, etching,
or flame-treating to modify the properties of a surface in order to achieve better adhesion.
Solvent-based bonding agents (primers) are also often used to improve adhesion.
However, these processes tend to be labor-intensive and/ or harmful to the environment. This is a major difference between these processes and plasma treatment, which is an efficient, more environmentally friendly alternative.
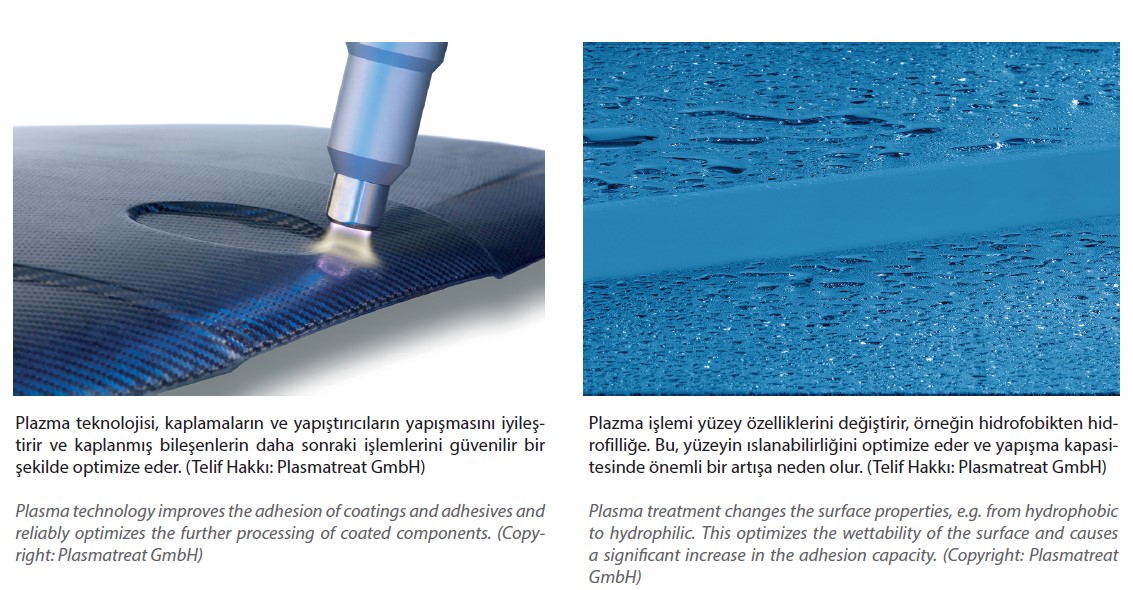
The second area of application in this field is the treatment of painted surfaces for bonding. This process is becoming increasingly important for bonding various components together in a range of different industrial sectors.
In many industries, and in the automotive and aviation industries in particular, these processes must be one hundred percent reliable – because if adhesive bonds fail, the consequences can be dire.
Surface coatings generally contain a series of additives to lend the surface certain properties, such as a high-gloss finish, scratch-resistance, resistance to dirt, and more. One thing these paints share, however, is their low surface energy, which hampers the formation of strong adhesive bonds.
Plasma technology allows you to overcome this hurdle by using Openair-Plasma for surface activation and adding a PlasmaPlus coating to improve adhesion – or in many cases, to make adhesion possible in the first place.
Benefits of Using Plasma Technology as Compared to Other Processes?
Comparing the processes that are used to improve paint adhesion on various substrates such as metal, plastic, wood, glass, ceramic, or fiber-reinforced polymer (FRP), plasma treatment is the most versatile pretreatment method: Unlike other processes, it can be used for all materials and surfaces. Its targeted use is another major advantage: Plasma jets allow the surface properties of the substrate to be selectively modified, so that only the relevant areas are targeted and there is no need to pretreat the entire surface.
The speed, distance of the jet heads to the substrate, and intensity of the plasma beam are precisely adjusted to the surface to be treated. This ensures consistently high quality and precise reproducibility of processes.
Determining the optimum parameters and providing specially adapted jet heads are among the core competencies of Plasmatreat. And unlike other processes, substrates pretreated with plasma can be processed further immediately after the plasma treatment.
Another benefit of plasma technology is how environmentally friendly the process is: While a process like flame treatment uses propane or methane gas, plasma jets are operated with electricity and compressed air.
And if you use electricity from renewable sources, plasma treatment is actually carbon neutral. PT-Bond is a special PlasmaPlus coating process; it is used to achieve a better adhesive bond and also replaces the use of primers that are harmful to the environment and human health, thereby avoiding VOC emissions.
Additionally, it is important to our industrial customers that our systems can be seamlessly integrated into existing production lines. Our innovative control systems ensure process control and reproducibility. On balance, the decisive advantage for our users is that they can choose the paint they want based on its primary purpose – ensuring adhesion to the substrate or during the bonding process is our job.
Real-world Examples of the Versatility of Plasma Technology Applications
The range of applications for plasma is essentially limitless. One major area of use is the automotive segment. Wellknown vehicle manufacturers use the Openair-Plasma technology and PlasmaPlus coatings for painted surfaces as an alternative to traditional treatment options.
One example is the activation of automotive paint before the application of EPDM door seals. Openair-Plasma is a costeffective, environmentally friendly alternative to solventbased primer as part of a fully automated process here.
And there are a number of other examples from our portfolio: We helped a manufacturer of premium watches use Openair-Plasma to create long-lasting prints on the dials of its products without damaging the sensitive dials during pretreatment.
In the metal can industry, we help to create long-lasting, stable adhesive bonds between a newly developed UV paint and the tinplate used in can manufacturing. By switching to UV-curing paints – a switch made possible by plasma technology – our customer benefits from faster production processes, higher productivity, and significant cost and energy savings.
At the same time, this modern process is safe for the environment and the natural world.
In the electronics industry, Openair-Plasma pretreatment is used for cleaning and activating printed circuit. Special potential-free jets are used to avoid damaging the sensitive electronics. The examples are endless: From battery manufacturing to the toy industry – Plasmatreat is active in nearly every sector imaginable.
Hakan Sağkal
General Manager
Plasmatreat Türkiye