Havacılık Sektöründe Boya Sistemleri
Havacılık Sektörünün Boya Sistemlerindeki İstek ve Beklentileri
Havacılık endüstrisi; ticari hava taşımacılığı, askeri havacılık, genel havacılık ve uzay sektörü olmak üzere dört bölümde kategorize edilmektedir.
Hava taşımacılığı, hava ulaşım ağlarının sayısının artması ve havacılık teknolojisinde yaşanan gelişmeler ile hızla büyüyerek dünya ekonomisine belirgin oranda katma değer yaratmaktadır.
Geldiği konum itibari ile hava taşımacılığı, küresel gelişimin önemli göstergelerinden
biri sayılmaktadır. Küresel havacılık pazarının, 2030 yılına kadar her yıl %5,9 oranında büyümesi öngörülmektedir (1).
ESPAS raporuna göre, küresel büyüme hızının %4,4 oranını geçmeyeceği göz önüne alındığında sektörün artan önemi belirgin hale gelmektedir (2).
Sivil havacılık sektöründe dünyanın lider konumundaki Boeing ve Airbus firmaları yolcu uçağı kategorisinde pazar hâkimiyetini ellerinde bulundurmaktadır (3).
Airbus tarafından yayınlanan tahmin raporuna göre 27.848 yeni uçak talebi olmakla birlikte bu taleplerin 26.921 adet yolcu ve 927 adet kargo uçağı olacağı öngörülmektedir.
Ülkemizde ve dünyada Covid-19 pandemisi sebebiyle getirilen kısıtlamaların kaldırılmasıyla birlikte, önümüzdeki 20 yıl süresince yolcu trafiğindeki artışın ise Boeing tahminlerine göre senelik %5,1 olacağı öngörülmektedir (4,5).
Havacılık sektöründeki son kullanıcıların artan talebi hava sanayiine yönelik boya pazarına yön vermektedir. Günümüzde sektördeki boya ihtiyacı çevresel etmenlerin de etkisi ile artış göstermiştir.
Havacılık boya pazarının 2021’den 2031’e kadar 1,4 milyar ABD dolarından 2 milyar ABD doları seviyelerine ulaşması tahmin edilmektedir (6).
Alüminyum, alüminyum alaşımları ve kompozit plastikler hafif olmaları ve yüksek dayanıma sahip olmaları sebebi ile uçak boya sistemlerinde yaygın olarak kullanılan yüzey malzemeleridir. Magnezyum, nikel, kobalt, bakır ve titanyum içeren alüminyum alaşımları havacılıkta kullanılmaktadır.
Alaşımlama işlemi ile saf alüminyuma kıyasla mekanik özellikler geliştirilirken, korozyon direnci ise düşmektedir. Uzay ve havacılık sanayinde yaygın kullanımı olan Al 2024 alaşımı
korozyona uğramaya müsait bir alaşım olmasına rağmen üstün fiziksel performansı sebebiyle tercih edilmektedir.
Bu yüzey malzemeleri için yüksek korozyon dayanımı ve yüzeye mükemmel yapışmanın sağlanması gerekmektedir. Alüminyum yüzeylerde yüksek yapışma elde edebilmek ve korozyon direncini arttırmak amacı ile yüzeyler bazı işlemlerden geçirilmelidir.
Alüminyum havadaki oksijen veya diğer oksitleyicilerin etkisi ile çok kolay paslanır ve yüzeyde oluşan alüminyum oksit molekülleri yüzeye sağlam bir şekilde tutunarak geçirimsiz bir tabaka oluşturur. Böylelikle altta kalan alüminyum tabakasının paslanması önlenir (7).
Alüminyum yüzeyler elektrokimyasal yöntem kullanılarak alüminyum oksitle homojen olarak kaplanabildiği (anodizasyon) gibi, kromat bazlı sıvılar ile yüzey işlemi gerçekleştirilebilmektedir.
Fakat kromatın insan sağlığı ve çevre üzerindeki zararlı etkileri göz önüne alındığında; kromatsız, alüminyum ve kompozit yüzeylerde yapışma performansını aynı oranda arttırabilen zirkonyum esaslı yüzey işlemlerinin kullanılması konusu gündeme gelmiştir (8).
Uçak yüzeyine uygulanan boya sisteminin temel amacı korozyon ve aşınmanın etkisini en aza indirerek uygulandığı aracın zorlu koşullara dayanmasını sağlamaktır.
Hava taşıtında korozyon, yapısal bütünlüğü zayıflatarak güvenlik problemleri ve onarımda yüksek maliyetlere sebep olabilir. Korozyon, metal malzemelerin içinde bulundukları ortamla
yaptıkları kimyasal ve elektrokimyasal reaksiyonlar neticesinde metalik özelliklerinin bozulmasına yol açan, doğal olarak gerçekleşen bir süreçtir.
Elektronik bir iletken (elektrot) ve iyonik bir iletken (elektrolit) arasında gerçekleşen
reaksiyonlar elektrokimyasal bir hücre oluşturur. Bu hücrenin temel elemanları anot, katot, fiziksel temas elemanı ve elektrolit çözeltisidir.
Metal yüzeylere uygulanan boya sistemlerinin temel görevi bir elektrot gibi davranan metal
yüzey ile yüzeye temas eden tuzlu su vb. gibi elektrolitler arasında bir bariyer katmanı oluşturmaktır.
Metal yüzeyinde safsızlık, kir, çizik veya çatlak bulunması halinde yüzeyde potansiyel bir fark oluşur ve bu durum korozyon sürecinin başlaması için yeterlidir.
Yüzeydeki bazı bölgeler anot, bazı bölgeler de katot gibi davranarak korozyon hücreleri oluşturur. Anotta yükseltgenme reaksiyonu ile metal atomları iyon halinde elektrolite geçer ve anot korozyona uğrar.
Yükseltgenme reaksiyonu sonucu açığa çıkan elektronlar; asidik ortamlarda hidrojen iyonunun indirgenmesinde kullanılarak hidrojen gazı açığa çıkarırken, nötral veya çözünmüş
oksijenin olduğu ortamlarda ise oksijen molekülünün indirgenmesinde kullanılarak hidroksil iyonları oluşturur.
Eş zamanlı gerçekleşen bu reaksiyonlar sonucu oluşan iyonlar metal yüzeyine yakın bölgede birleşerek çökelir ve pas oluşturur (9).
AMS 3095 şartnamesinde performans testi olarak yer alan filiform korozyonu kabuk altı korozyonunun bir türüdür ve havacılıkta önemli bir sorun olarak değerlendirilir.
Filiform korozyonunu mekanizması boyalı yüzeyin zayıf noktasından başlayarak kabuk altında yatay iplikler halinde ilerleme şeklindedir. Alüminyum yüzeylerde %70-95 relatif nem ve 20-40°C sıcaklıkta gerçekleşir.
Bu korozyon türünün başlaması için boyalı yüzeyin klorür, sülfat ve karbonik asit gibi kirleticilere maruz kalması ön koşuldur. Boyalı yüzeyin zayıf noktasından su ve oksijen girişi gerçekleşir.
Metal yüzey elektron vererek metal iyonlarını oluşturur ve bu iyonlar su ile reaksiyona girerek hidrojen iyonlarının (H+) oluşmasına sebep olur. H+ iyonu ortamdaki klorür, sülfat gibi iyonları çekerek ipliğin uç kısmına osmotik etkiyle daha çok su girmesini tetikler.
Aktif olmayan kuyruk kısmında ise su uzaklaştırılır. Korozyonun başlangıç noktasında oksijen seviyesi en yüksek değerdeyken, korozyonun ilerlediği doğrultuda konsantrasyon giderek düşer.
Korozyon sonucu uç kısımda metal hidroksit ve hidrojen iyonları oluşur. Bu ürünlerin
oluşması ile uç kısımda oksijen konsantrasyonu azalır ve pH değeri düşer. Korozyonun devamlılığı bu şekilde uç noktadan ileriye doğru gerçekleşir (10).
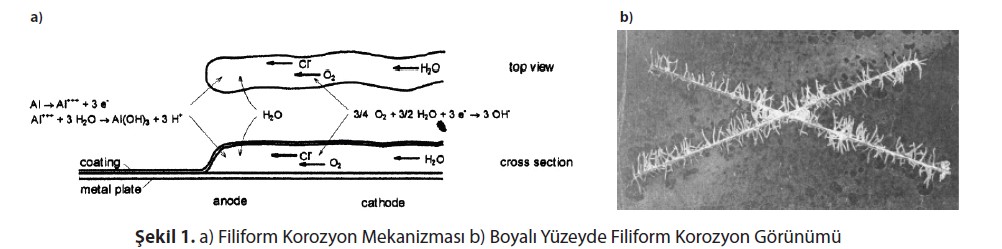
Havacılık astarlarında alüminyum yüzeylerde etkin korozyon dayanımını sağlamak amacıyla +6 değerlikli krom içeren stronsiyum kromat esaslı antikorozif pigmentler kullanıldığı
görülmektedir.
Stronsiyum kromat çevre ve insan sağlığı üzerinde yarattığı tehdit ile tehlikeli madde listesinde yer almış ve kanserojen olma sebebi ile özel sağlık tehlikesi yaratan maddeler listesine girmiştir. Havacılık sektöründe kullanımı kısıtlanmış, havacılık dışında kullanımı ise
yasaklanmıştır. Bu nedenle krom içermeyen, çevre dostu astarlar geliştirilmektedir (11).
Havacılıkta ağırlık ve korozyon gibi etkilerden ötürü kompozit malzemeler alüminyum yüzeylere alternatif olmaya başlamıştır. Kompozit panel uygulamalarında zımparalama ve
yüzey işçiliği kolaylığı ile yüzey kusurlarını kapatma özelliği yüksek olan boyalar tercih edilmeye başlanmıştır.
Havada uçuşan partiküller ve yağmur damlaları gibi etkenler yüksek hıza sahip araçlarda erozyona sebep olmaktadır. Alüminyum ve kompozit gibi havacılık malzemelerinin erozyona
karşı dayanımı zayıftır.
Bu durum aerodinamik yapının kritik olduğu hava araçlarında korozyon ve yapısal yönlerden
ciddi zafiyetlere yol açabilmektedir. Erozyon uçak yüzeyinin radom, kanat hücum kenarı, uçak gövdesinin geri kısmındaki yatay kanatları gibi belirli bölgelerde daha sık gözlenir.
Partikül erozyonu, katı bir parçacığın çarptığı bir yüzeyden materyal kopardığı dinamik bir süreçtir. Hava araçlarının bulunduğu irtifalarda partiküllerin az olması ve yağmur damlalarının yıkıcı etkisinin daha yüksek olması nedeniyle havacılıkta yağmur erozyonu daha fazla önemsenmektedir.
Yağmur erozyonunda sıvıların sıkıştırılamaması sebebiyle çarpma anında damla içerisinde “Su Çekiç Etkisi” olarak belirtilen süpersonik bir şok dalgası oluşur. Yüksek hızla katı
bir yüzeye çarpan yağmur damlaları, yüzeye paralel biçimde hızını katlayarak hareket eder (yatay jet) ve kaplama yüzeyindeki girinti ve çıkıntılara (yüzey kusurlarına) çarparak kaplama filmini aşındırır.
Bu nedenle su, katı taneciklere oranla daha fazla hasara neden olur. Yağmur erozyonuna dayanıklı kaplama geliştirmede, oluşan şok dalgasının sönümlenebilmesi malzemenin elastikiyetine bağlıdır.
Kaplama yüzeyindeki pürüzlülük azaldıkça su jetinin yıkıcı etkisi de azalır. Kaplamaların yapışma mukavemetinin yüksek olması erozyonun engellenmesinde etkendir (12,13).
Sivil havacılık ve askeri havacılık sektörüne yönelik boyaların sahip olması gereken teknik nitelikler standartlarca tanımlanmıştır.
Sivil havacılık uçak gövdesi dış cephe boyası için, Otomotiv Mühendisleri Birliği’nin tanımlamış olduğu “AMS 3095 Boya: Havayolları İçin Yüksek Parlaklıklı Dış Cephe” standardı kabul edilmektedir.
Bu standart Al 2024 alaşımı üzerine uygulanan boyaların özellikleri ve performans
parametrelerini içermektedir. Askeri havacılık için de benzer maddeleri içeren standartlar ülkelerin savunma sanayiine yön veren kuruluşları tarafından hazırlanmaktadır.
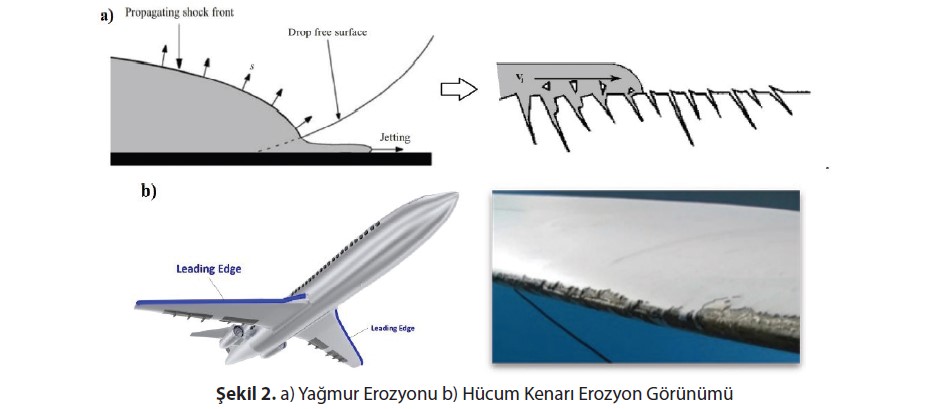
Uçak boya sisteminin fosfat ester yapısındaki reaktif kimyasal olan hidrolik sıvılarına, yağlara ve yakıtlara karşı dirençli olması gerekmektedir.
Hava aracı uçuş sırasında -50°C ve daha düşük sıcaklıklara ulaşmakla birlikte, yüksek irtifalarda daha fazla ultraviyole (UV) radyasyona maruz kalmaktadır.
Hava taşıtının ömrünü uzatmak ve uçuş emniyetini artırmak için; düşük sıcaklıklarda yüksek elastikiyete sahip ve UV radyasyon direnci yüksek boya sistemleri kullanılmalıdır.
Boya sistemi toz, yağmur veya yağmurla karışık kar gibi maruziyetlere karşı mükemmel aşınma direncine sahip olmalıdır.
Ayrıca uçuş sırasında sürtünmeyi en aza indirmek için boyalı yüzeyin pürüzsüz olması gerekmektedir. Burada önemli nokta, çapraz bağ yoğunluğu arttıkça elastikiyet ve aşınma direnci özelliklerinin geri gittiğidir (8).
Uygulanan boyanın kalınlığı ağırlık sebebi ile uçak ve bileşenlerinin kalitesini doğrudan etkilemekle birlikte enerji maliyeti için de hassas bir parametredir. Bu sebeple boyanın sahip olması gereken tüm performans özellikleri düşük film kalınlıklarında sağlanmalıdır.
Uçak boya sistemlerinde alüminyum yüzeylere iyi yapışan, korozyon dayanımı yüksek olan ve amin ile kürlenen düşük çapraz bağ yoğunluğu oluşturacak epoksi astarlar kullanılmaktadır.
Düşük çapraz bağ yoğunluğu yüksek elastikiyet sağlar ve hangarlardaki boya söküm aşamasında kaplamanın uçak yüzeyinden sökülebilmesini kolaylaştırır. Astar üzerine uygulanan iki komponentli poliüretan kaplamaların yüksek parlaklık, görüntü netliği ve yüksek dış dayanıma sahip olması gerekmektedir.
Bu kaplamaların kimyasal malzemelere dayanım sağlaması için yüksek çapraz bağ yoğunluğuna sahip olması gerekir. Uçak boya sistemleri yüksek miktarda solvent içermektedir. Uçucu Organik Bileşik (VOC) emisyonunun düşürülmesi, sağlık riskleri ve çevre kirliliği nedeniyle üzerinde durulan önemli bir konudur.
Ayrıca havacılık şartnamelerinde belirtilen VOC limitlerini sağlamak amacıyla su bazlı sistemlerle ilgili çalışmalar da ağırlık kazanmıştır (8).
Kanat Boyacılık Tic. ve San. A.Ş., savunma ve havacılık bölümüne özel bir birim kurarak, sivil ve askeri havacılık boyaları alanında uzmanlaşmakta ve sektörden gelen talepleri karşılamaktadır. Geliştirilecek ürün gamı ile ülke ekonomisine destek vererek yerlileşme ve millileşme politikasına katkı vermeyi hedeflemektedir.
Kaynaklar
(1) https://www.embroker.com/blog/aerospace-market-growth-strategies/
(2)https://espas.secure.europarl.europa.eu/orbis/sites/default/files/generated/document/
en/The%20Global%20Economy%20in%202030.pdf
(3) https://thinktech.stm.com.tr/tr/sivil-havacilik-sektor-degerlendirmesi-
(4) Çizmecioğlu, M. (2013). Türkiyede sivil havacılık ve hava yolu ulaşımı üzerine bir
araştırma (Master’s thesis, Fen Bilimleri Enstitüsü).
(5) S. H. G. M (2021). Sivil Havacılık Genel Müdürlüğü Faaliyet Raporu 2021. TC Ulaştırma
ve Altyapı Bakanlığı, Ankara.
(6) https://www.factmr.com/report/aerospace-coatings-market
(7) Tunçgenç, M. (2004). Genel Boya Bilgileri.Akzo Nobel Kemipol
(8) Goldschmidt, A., & Streitberger, H. J. (2003). BASF handbook on basics of coating technology. William Andrew.
(9) Davis, J. R. (Ed.). (2000). Corrosion: Understanding the basics. Asm International.
(10) Delplancke, J. L., Berger, S., Lefebvre, X., Maetens, D., Pourbaix, A., & Heymans, N.
(2001). Filiform corrosion: interactions between electrochemistry and mechanical
properties of the paints. Progress in organic coatings, 43(1-3), 64-74.
(11) Jones, F. N., Nichols, M. E., & Pappas, S. P. (2017). Organic coatings: science and
technology. John Wiley & Sons.
(12) Elhadi Ibrahim, M., & Medraj, M. (2019). Water droplet erosion of wind turbine
blades: Mechanics, testing, modeling and future perspectives. Materials, 13(1), 157.
(13) Valaker, E. A., Armada, S., & Wilson, S. (2015). Droplet erosion protection coatings for
offshore wind turbine blades. Energy Procedia, 80, 263-275.
Begüm Özyağcı Tokgöz
Ar-Ge Kimyageri
Kanat Boya