Gıda Ambalaj Korozyon Kontrolünde Elektrokimya – Kaplamalı Alüminyum Örneklerinde Elektrokimyasal Empedans Spektroskopisi
Gıda ve meşrubat endüstrilerinde üretilen yiyecek ve içeceklerin raf ömrü, büyük oranda ambalajlama şekli ve kullanılan ambalajlama malzemesinin türüne bağlıdır.
Metaller, farklı pasifleştirici gıda sınıfı katmanlar ile kaplanabilmeleri nedeni ile özellikle bu amaç için ideal materyaller olarak öne çıkmaktadır. Metal ambalajlama, gerek ısıl işlemler ve gerekse depolama aşamalarında mükemmel fiziksel koruma ve bariyer özellikleri sağlamanın yanı sıra, şekillendirilebilirlik, dekoratif potansiyel, geri dönüştürülebilirlik ve tüketici kabulünün mükemmel bir kombinasyonunu sunmaktadır.
Metal ambalajlamada farklı birçok malzeme kombinasyonu mevcut olmak ile birlikte, gıda ve meşrubat endüstrilerinde en çok kullanılan materyallerin başında çelik ve alüminyum gelmektedir. Özellikle alüminyumun farklı formlarda kullanım şekilleri mevcuttur.
Saf Alüminyum
Tipik olarak teneke kutu, folyo, lamine kâğıt veya plastik ambalajlama için kullanılan alüminyum, boksit cevherinden elde edilen hafif, gümüşi beyaz bir metal olup, alümina ve oksijenin kombinasyonu formunda bulunmaktadır. Birçok metalin aksine, alüminyum birçok korozyon türüne karşı oldukça dirençlidir; doğal alüminyum oksit kaplaması, hava sıcaklığı, nem ve kimyasal bozulma etkilerine karşı oldukça etkili bir koruma sağlamaktadır.
Alüminyum, nem, hava, koku, ışık ve mikroorganizmalara karşı mükemmel bir bariyer sağlamanın yanı sıra, iyi bir esneklik ve yüzey direncine, mükemmel dövülebilirlik ve şekillendirilebilirliğe ve aynı zamanda da olağanüstü bir kabartma potansiyeline sahiptir.
Aynı zamanda alüminyum geri dönüştürülmesi ve yeni ürünlere dönüştürülmesi kolay olduğu için geri dönüşüm prosesleri için de ideal bir malzemedir. Saf alüminyum, tipik olarak meşrubat kutuları, evcil hayvan gıdaları, deniz ürünleri ve önceden diş açılmış kapakların hafif ambalajlanması için kullanılmaktadır.
Alüminyum Folyo
Alüminyum folyo, saf alümina metalin çok ince tabakalar halinde sarılması ve sonrasında haddelenerek ölükatlanma (film üzerinde bir çukur veya katlama oluşturulduğunda yerinde kalır) özellikleri verilmesi yolu ile elde edilmektedir. Böylece alüminyum folyo oldukça sıkı bir şekilde katlanabilmektedir.
Alüminyum folyonun, yiyecekleri sarmak için kullanılan ince tabakalardan tepsilere sermek için kullanılan daha kalın yapraklara kadar uzanan geniş bir yelpazeye yayılmış farklı kalınlıkta türleri bulunmaktadır. Tüm alüminyum ambalajlarda olduğu gibi, alüminyum folyo da nem, hava, koku, ışık ve mikroorganizmalara karşı mükemmel bir bariyer koruması sağlamakta, asidik gıdalara karşı inert yapıya sahip olmanın yanı sıra herhangi bir cila veya koruma gerektirmemektedir.
Alüminyum Laminatlar ve Metalize Filmler
Ambalajların laminasyonu, genellikle alüminyum folyonun kâğıt veya plastik filme bağlanması ve böylece bariyer özelliklerinin geliştirilmesi prensibine dayanmaktadır. Plastiğe yapılan laminasyon ısı yalıtımı sağlıyor olsa da nem ve havayı tamamen engellememektedir. Lamine edilmiş alüminyumun nispeten pahalı olması nedeni ile bu teknik genellikle kurutulmuş çorbalar, baharat ve otlar gibi yüksek değerli gıdaları ambalajlamak için kullanılmaktadır.
Lamine ambalajlara daha ucuz bir alternatif ise metalize filmlerdir. Metalize filmler ince bir alüminyum metal tabakasına sahip plastiklerdir (Fellows and Axtell 2022).
Bu filmler nem, yağlar, hava ve kokulara karşı geliştirilmiş bariyer özellikler sunmakta ve alüminyumun oldukça yansıtıcı olan yüzeyi tüketicilere oldukça çekici gelmektedir.
Metalize filmler lamine filmlere oranla daha esnek olmaları nedeni ile ağırlıklı olarak atıştırmalıkların ambalajlanmasında kullanılmaktadır. Laminatlar ve metalize filmlerin bileşenlerinin ayrı ayrı geri dönüştürülmesi teknik olarak mümkün olsa da söz konusu materyallerin ayrılmasındaki zorluk ekonomik olarak uygulanabilir bir geri dönüşümü zorlaştırmaktadır.
Korozyon
Korozyon, bir metalin bozulma sürecini tanımlamak için kullanılan genel bir terimdir. Korozyon olaylarının önemli bir bölümü elektrokimyasal nitelikte olup metal yüzeyinde en az iki reaksiyon gerçekleşmektedir.
Söz konusu reaksiyonlardan ilki anodik kısmi reaksiyonu olarak da adlandırılan oksidasyon (örn. demirin çözünmesi), diğeri ise katodik kısmi reaksiyonu olarak adlandırılan bir indirgenme reaksiyonudur (örn. oksijenin indirgenmesi).
Elektrokimyasal reaksiyonların ürünleri, nihai ürünü oluşturmak için birbirleriyle elektrokimyasal olmayan bir şekilde de reaksiyona girebilmektedir.
Gıda ve meşrubat ambalajlama proseslerinde metal kullanımı, korozyon süreçlerinden etkilenebilmektedir. Korozyon, hem ambalajın atmosfer ile temas eden tarafında hem de ürün içeriğine maruz kalan tarafında gerçekleşebilmekte ve bu nedenle metal ambalaj yüzeyleri çeşitli kaplama ve/veya cilalama işlemlerine tabi tutulmaktadır.
Metal ambalajlamada korozyon süreçlerinin incelenmesi için en yaygın yollardan biri de metal ambalajın ve/veya kullanılan kaplamaların elektrokimyasal yapısının değerlendirilmesidir.
Bu çerçevede, hızlı sonuç vermesi ve tahribatsız doğası ile Elektrokimyasal Empedans Spektroskopisi (EIS) kaplama endüstrisinde kullanılan ilginç analiz tekniklerden biri olarak karşımıza çıkmaktadır.
Elektrokimyasal empedans spektroskopisi (EIS), bir alternatif gerilim (potansiyostatik EIS) veya akım (galvanostatik EIS) tarafından bozulan bir sistemin lineer yanıtını araştırmak için kullanılan güçlü bir tekniktir. EIS, korozyon süreçlerinin polarizasyon direnci ve zaman sabitleri hakkında bilgi elde etmek için yaygın olarak uygulanmaktadır.
Bu inceleme yazımızda farklı kaplamalara sahip üç farklı alüminyum plaka üzerinde gerçekleştirilmiş EIS analizlerini yakından inceliyor olacağız.
Deneysel İçerik
Bu çalışmada Al2O3 ile kaplanmış 3 farklı alüminyum plaka örneği test edilmiştir. Örneklerin ikisinde ek kaplama tabakaları bulunmaktadır. Ek kaplamamaların tam bileşimi hakkında ayrıntılı bilgi bulunmaması nedeni ile bu iki kaplama ”pembe” ve “altın“ kaplamalar olarak anılacaktır.
[caption id="attachment_129606" align="aligncenter" width="599"]
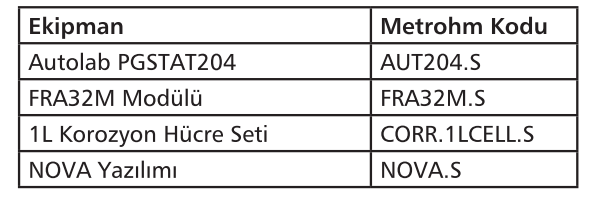
Tablo 1: Kullanılan ekipman ve yazılım[/caption]
Her bir levha Şekil 1’de gösterilen ASTM uyumlu 1 L’lik Metrohm Autolab korozyon hücresinin numune tutucusuna uyacak şekilde 1.5 cm çapında diskler elde etmek üzere kesilmiştir. Ölçümlere maruz kalacak alan 1 cm2 olarak belirlenmiştir.
Kaplama tabakalarını çıkartmak ve numune tutucu ile iyi bir elektrik teması sağlamak için her numunenin bir tarafı 600 kumlu zımpara kağıdı ile parlatılmıştır. Tüm ölçümler, 33 g NaCl’nin bir litre ultrasaf suda çözülmesiyle elde edilen yapay deniz suyu kompozisyonu içinde gerçekleştirilmiştir.
[caption id="attachment_129607" align="aligncenter" width="573"]
Şekil 1: 1 L’lik korozyon hücresi ve FRA32M modülü entegre PGSTAT204[/caption]
Paslanmaz çelik bir karşıt elektrot ve 3 M KCl elektrolit ile doldurulmuş bir Ag/AgCl referans elektrot kullanılarak üç elektrot sistemi tamamlanmıştır. Bu çalışmadaki tüm potansiyel değerler, referans elektrodun potansiyeline göre verilmiştir. Elektrotlar, Şekil 1’de gösterilen FRA32M empedans modülü entegre bir Metrohm Autolab PGSTAT204 potansiyostat/galvanostat sistemine bağlanarak ölçümler alınmıştır.
Prosedür
Kademeli çözünme ölçümü (SDM), alüminyum lehimleme levhalarının korozyon özelliklerini test etmek için kullanılan elektrokimyasal bir tekniktir. SDM tekniği kısaca aşağıdaki basamakları içermektedir:
• Beş dakika boyunca açık devre potansiyeli (OCP) kaydedilir.
• OCP’ye karşı 20 mV potansiyel artırılır ve sistem 30 dakika boyunca polarize edilir.
• OCP beş dakika boyunca kaydedilir. Son iki komut, yaklaşık 7 saatlik bir süre boyunca 12 kez tekrarlanır. OCP’ye karşı döngü numarası grafiği oluşturulur.
Bu uygulamada SDM öncesinde ve sonrasında EIS ölçümleri alınmıştır. 10 mV (rms) genlik sinyali, 100 kHz ila 10 Hz frekans aralığında, logaritmik frekans adımı içeren ve her ondalıkta 10 frekans içeren, açık devre potansiyeli üzerine (OCP) bindirilmiştir.
SDM’den önceki ve sonraki veriler karşılaştırılmış ve uygun eş değer devreler ile çakıştırılmıştır. SDM, EIS prosedürleri ve data işleme aşamaları NOVA yazılımı kullanılarak gerçekleştirilmiştir.
Eşdeğer Devreler
Elektrokimyasal Empedans Spektroskopisi’nde metal substratlar ve üzerlerinde yer alan kaplamaların yapısal özellikleri, elde edilen ölçüm sonuçlarının “Fit & Simulation” işlemlerine tabi tutulması ve yorumlamayı takiben elektriksel eş değer devreler ile temsil edilmektedir.
İncelenmekte olan örnek ile ilgili uygun bir eş değer devrenin tespit edilebilmesi, sistem hakkında daha derin bilgilere gereksinim duymaktadır. Farklı kaplama türleri ve bunlara karşılık gelen eş değer devreler hakkında temel bazı tanımlayıcı bilgiler aşağıda sunulmaktadır.
İdeal durumda, iletken olmayan kaplama metal substrat üzerine mükemmel bir şekilde bağlanmakta ve herhangi bir yüzey kusuru içermeyen mükemmel bir kaplama arayüzü elde edilmektedir. Bu durum, Şekil 2’de gösterilen ve kaplama tabakasının CL kapasitansı ile seri olarak kompanze edilmemiş direnci RΩ olan bir eş değer devrenin tanımladığı bir blokaj elektroduna yol açmaktadır.
[caption id="attachment_129608" align="aligncenter" width="445"]
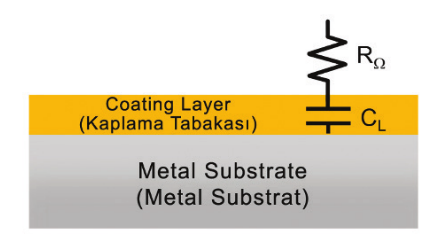
Şekil 2: İdeal, metal substrat üzerinde kusursuz bir iletken olmayan kaplama ve karşılık gelen RΩCL eş değer devresi.[/caption]
Gerçek hayatta ise, yüzey kusurlarına sahip bir kaplama daha yaygın bir durumdur. Bu tür kusurlar, Şekil 3’te gösterilen ve yukarıda belirtilen RΩ CL devresi ile temsil
edilen kaplanmış alanın kaplanmamış bir yüzey (genel bir faradaik empedans Zf
ile paralel bir çift katmanlı kapasitans Cdl ile modellenir) ile birlikte yer aldığı mükemmel olmayan bir kaplama şeklinde ortaya çıkabilir. Ortaya çıkan eş devre yine Şekil 3’te gösterilmektedir.
[caption id="attachment_129609" align="aligncenter" width="406"]
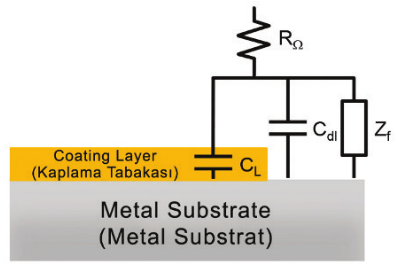
Şekil 3: Kısmi kaplamaya sahip bir metal substrat ve eş değer devresi.[/caption]
Yüzey üzerinde yer alan gözenekler de kaplama tabakasının kusurları arasında yer almaktadır. Bir gözenek, Şekil 3’teki gibi, substratın kaplan-mamış olduğu bir bölüm olarak değerlendirilebilir, ancak kendisi ve yığın (bulk) arasındaki elektrolit alışverişini engelleyecek kadar da küçük boyuta sahiptir.
Bu nedenle gözeneklerin içindeki iyon konsantrasyonu yığından farklı olabilmektedir. Bu durum, RΩ yığın elektrolit direncinden farklı bir RL direnci ile sonuçlanır. Şekil 4’te, gözeneklerin varlığı ve bu çerçevede ilgili eş değer devre gösterilmektedir.
[caption id="attachment_129610" align="aligncenter" width="450"]
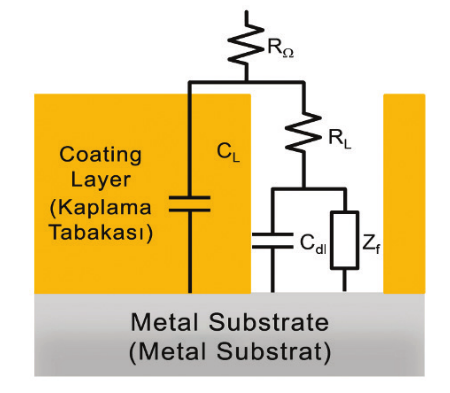
Şekil 4: İletken olmayan gözenekli bir kaplama ve eş değer devresi.[/caption]
Son olarak, ilk katman üzerine yerleştirilen bir dış kaplamanın varlığı da dikkate alınmalıdır. Bu üst katman sisteme ikinci bir arayüz eklemekte ve bir ek RL2
direnci ile paralel CL2 çift katmanlı kapasitansı ile modellenmektedir. Ortaya çıkan final sistem ve eş değer devre Şekil 5’te gösterilmektedir.
[caption id="attachment_129611" align="aligncenter" width="352"]
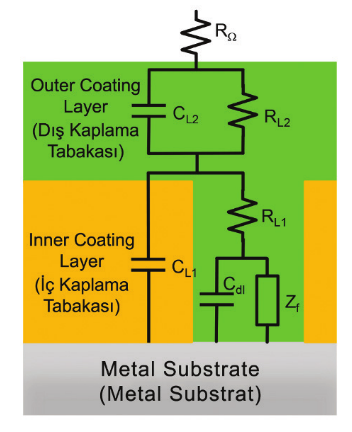
Şekil 5: İki iletken olmayan gözenekli kaplama ve eş değer devresi.[/caption]
Genel empedans Zf ile ilgili olarak, uygun devre elemanını seçebilmek için elektrolite maruz kalan kaplama katmanlarının bileşimini ve davranışlarını bilmek önem taşımaktadır Bu tür devre elemanlarına tipik örnekler, sabit faz ve Warburg difüzyon elemanlarıdır.
Ölçüm Sonuçları
Tüm ölçümlerde gözeneklerin var olduğu kabul edilmiştir. SDM öncesi elde edilen verilerin fitting işlemleri esnasında yukarıda belirtilen eş değer devreler değerlendirilmiştir. Oksit kaplı örnek plakası için Şekil 4’te yer alan eş değer devre seçilirken, “altın” ve “pembe” kaplamalı örnekler için Şekil 5’te yer alan eş değer devre kullanılmıştır.
Aşağıdaki bölümlerde, üç örneğin SDM’den önce ve sonraki Nyquist grafikleri gösterilmektedir. Her bir Nyquist grafiği için, mavi noktalar deneysel verileri ve siyah çizgi ise grafiğin içinde çizilmiş olan eş değer devre ile gerçekleştirilen örtüşmeyi temsil etmektedir. Bu incelemede sadece deneysel veriler ışığında yukarıda atıfta bulunulan modeller ile ilintili seçilen eş değer devreler değerlendirilmekte olup, devre elemanlarının rakamsal değerleri tartışma dışı bırakılmıştır.
Alüminyum Oksit
Şekil 6’da, oksit örneğinin SDM’den önceki Nyquist grafiği gösterilmektedir. Seçilen eşdeğer devre, kaplamada gözeneklerin varlığını modellemek için kullanılan eş değer devreye benzemektedir (Şekil 4).
[caption id="attachment_129615" align="aligncenter" width="402"]
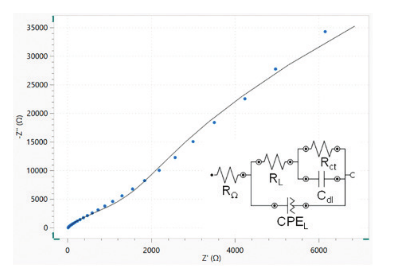
Şekil 6: SDM öncesi oksit numunesi Nyquist eğrisi[/caption]
Oksit tabakasının CL çift tabaka kapasitansı, yüzeyin pürüzlülüğünü hesaba katmak için bir (CPEL) sabit faz elemanı ile değiştirilmiştir. Genel empedans Zf ‘in Rct yük transfer direncine yakın olduğu tespit edilmiştir.
[caption id="attachment_129617" align="aligncenter" width="566"]
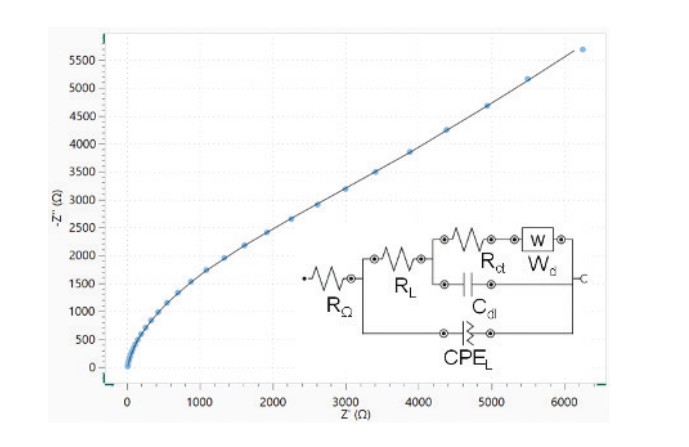
Şekil 7: SDM sonrası oksit numunesi Nyquist eğrisi[/caption]
SDM’den sonra, yani korozyon sürecinden sonra, oksit numunesinin Nyquist grafiği (Şekil 7) düşük frekanslarda 45°’lik bir çizgi göstermektedir; bu durum, gözenekler içindeki iyon difüzyonu ile ilişkili olabilir ve bir Warburg elemanı ile eşleştirilebilmektedir. İyonların, korozyon sürecinin bir ürünü olabileceği değerlendirilmektedir.
“Altın” Kaplamalı Alüminyum
Altın kaplamalı numunede ise, altın kaplamanın oksit tabakasının üzerine uygulandığı değerlendirildiği için iki tabakalı bir kaplama modeli seçilmiştir. Bu durum, Şekil 8’de gösterilen Nyquist grafiği ile temsil edilmektedir. Veri eşleştirmede kullanılan eş değer devrede de kapasitörler sabit fazlı elemanlarla değiştirilmiştir. Genel empedans Zf
, CPEdl sabit faz elemanı ile paralel Rct yük transfer direncinin bulunduğu bir arayüz olarak seçilmiştir.
[caption id="attachment_129620" align="aligncenter" width="463"]
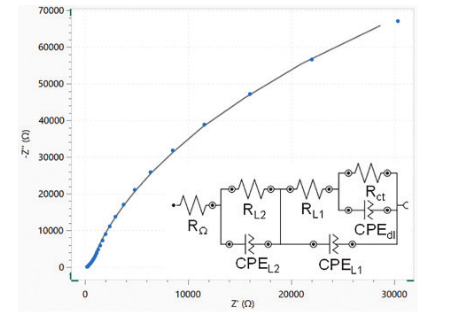
Şekil 8: SDM öncesi altın kaplamalı numune Nyquist eğrisi
[/caption]
Korozyon süreci, Şekil 9’daki Nyquist grafiğinden anlaşılacağı gibi, kaplamaların özelliklerini değiştirmektedir.
[caption id="attachment_129622" align="aligncenter" width="523"]
Şekil 9: SDM sonrası altın kaplamalı numune Nyquist eğrisi[/caption]
“Pembe” Kaplamalı Alüminyum Son örnekte, pembe tabaka, altın kaplı numunede olduğu gibi oksit tabakasının üzerine uygulanmıştır. Bununla birlikte, Şekil 10, SDM’den önce, Nyquist grafiğinin düşük frekanslarda neredeyse dikey bir çizgi olduğunu göstermektedir. En iyi örtüşme, Zf faradaik empedansının ihmal edilmesi ve metal ile oksit yüzeyi arasındaki arayüzü temsil eden seri bir sabit faz elemanı (CPEdl), eklenmesi ile sağlanmıştır. Bu durum kaliteli bir kaplama göstergesi olabilir.
[caption id="attachment_129623" align="aligncenter" width="455"]
Şekil 10: SDM öncesi pembe kaplamalı numune Nyquist eğrisi[/caption]
SDM’den sonra ise en iyi örtüşme CPEdl yerine çift katmanlı kapasitans Cdl
yerleştirilerek elde edilmekte ve Şekil 11’de gösterilmektedir.
Bu durum, kaplamanın diğer iki numuneye kıyasla SDM tarafından indüklenen korozyon sürecinden daha az etkilendiği ve alüminyum-gözenek arayüzünde herhangi bir faradaik işlem meydana gelmediği anlamına gelebilmektedir.
[caption id="attachment_129625" align="aligncenter" width="490"]
Şekil 11: SDM sonrası pembe kaplamalı numune Nyquist eğrisi[/caption]
Şekil 12’de üst üste gösterilen SDM’den sonraki üç Nyquist grafiği, pembe kaplamalı numune, oksit ve altın kaplamalı numunenin empedansları arasındaki karşılaştırmayı gözler önüne sermektedir.
[caption id="attachment_129626" align="aligncenter" width="462"]
Şekil 12: SDM sonrasında üç numunenin Nyquist eğrisi[/caption]
Bu bilgiler çerçevesinde, pembe kaplamanın, en azından SDM esnasında, korozyona karşı en iyi performansı sergilemekte olduğu görülmektedir.
Genel Sonuç
Elektrokimyasal Empedans Spektroskopisi (EIS), korozyon biliminde yaygın olarak kullanılan hızlı, tahribatsız ve güçlü bir tekniktir.
EIS, incelenen sistem hakkında ayrıntılı bilgi sağlanabildiğinde, kaplamaların korozyona karşı kalitesi hakkında önemli bilgiler verebilmektedir. Yukarıda detayları sunulan uygulama, NOVA yazılımına sahip bir Autolab PGSTAT204 sistemi ve bir Autolab 1 L korozyon hücresi kullanıldığında farklı malzemelerle kaplanmış alüminyum numuneler üzerinde EIS’nin nasıl gerçekleştirilebileceği ile ilgili ayrıntıları göstermektedir.
Metrohm elektrokimya grubu olarak bizler, Metrohm Autolab ve Metrohm DropSens markalarımız ile, her tür elektrokimyasal araştırmanın gereksinimlerini karşılamak için temel kompakt ve ekonomik sistemlerden çok kanallı proje istasyonları ve elektrokimya ile spektroskopik ölçümlerin kombine edilmesine olanak tanıyan tam entegre spektroelektro-kimyasal (UV-Vis, VisNIR ve Raman) plat-formlara kadar uzanan geniş bir yelpazede enstrüman, yazılım ve aksesuar seçenekleri sunabilmekteyiz.
Kaynaklar
1. Metrohm Elektrokimya White Paper, Electrochemistry in the quality control of food and beverage packaging 2. Metrohm Elektrokimya Uygulama Notu AN-COR-009, Electrochemical impedance spectroscopy of three coated aluminum samples
3. Metrohm Elektrokimya Uygulama Notu AN-COR-008, Stepwise dissolution measurement 4. K. Marsh, and B. Bugusu, “Food Packaging—Roles, Materials, and Environmental Issues”, Journal of Food Science, Vol. 72, Nr. 3, R39–R55, 2007.
Yeliz Yavuz Çevik
Ürün Müdürü
Metrohm Turkey