Galvanizing in Alkaline and Cyanide-Containing Electrolytes
With a share of about 20% of the galvanically coated total area in Europe, zinc is the second most important metal layer after nickel. Today it is separated by about 50% from acidic electrolytes, 30% from alkaline-cyanidefree and 20% alkaline-cyanide
This shows that the economic and eco-friendly use of alkaline electrolytes is still very important.
Alkaline cyanide-free, pyrophosphate and aminocomplex-containing electrolytes can be used for the electrolytic deposition of zinc and zinc alloys from alkaline media, cyanide, however, for various reasons, only cyanide-containing and alkaline-cyanide-free electrolytes have been used in operational practice.
Pyrophosphate- containing and so-called neutral electrolytes which contain amino and possibly other complexes are used only in exceptional cases. The most important constituents of the alkaline electrolytes are zinc salt, sodium hydroxide and in case of the cyanidic variants are involved, sodium cyanide.
In the electrolytes for alloy plating, compounds of particular alloying ingredients are to be added. In addition, usually small amounts of organic compounds are included, which have the function of brighteners.
Commercially supplied brighteners are often mixtures and contain, for example, compounds from the group of aldehydes, polymers such as polyepoxydamines, but in part also small amounts of compounds of nickel, selenium and other metals that promote gloss.
Tables 1 and 2 contain typical basic compositions of electrolytes for the seperation of zinc and zinc alloys. For clarity, the most important deposition parameters are listed in each case.
Alkaline cyanide electrolytes have long been used for galvanizing on an industrial scale and are therefore particularly well matured in their development. In addition to the frequently required high gloss, further controllable layer properties can be guaranteed in high quality.
The relevant technologies - processes and systems - have reached a very high level and allow a rational operation in both the rack and the barrel galvanizing. Nevertheless if someone tries to replace the cyanide-containing by alkaline-cyanide-free or weakly acidic process, this is due to the less expensive treatment of the wastewater and concentrates.
Of course, cyanide-containing wastewater can be treated so that they comply with the regulations on wastewater discharge. However, in addition to the special cyanide poisoning measures must be provided so that no slightly soluble cyanides will be formed in the reaction with any existing metallic impurities.
In cyanide oxidation it may also come to the known difficulties with the AOX formation. Therefore, if one wishes to take full advantage of the beneficial properties of the alkaline cyanide processes, while maximizing environmental friendliness, which means to ensure compliance with all legal requirements, some criteria must be taken into account. The most important are the following:
• Choosing the best method,
• Quality assurance during galvanizing,
• Bath proportions,
• Regenerating,
• Recycle of the electrolytes (circulation control).
1. Choosing of the Best Method
As already mentioned, about 50% of today’s galvanizing is done with acidic electrolytes. This is slightly due to the increase in strip galvanizing, which so far took place exclusively in acidic electrolytes.
The main reason, however, is that the barrel and rack zinc plating, which was formerly operated exclusively with cyanide electrolytes, was switched to acidic electrolytes.
This was made possible by the excellent properties of the weakly acidic galvanizing electrolytes developed in the 1970s which now matured. Nevertheless, there are still many cases in which alkaline electrolytes - whether in galvanizing or alloy deposition - can not be replaced.
The reasons for this lie in the electrolyte properties, especially the broad applicable current density range and the high throwing power of cyanide electrolytes, which are often indispensable in geometrically complicated parts and in the mass galvanizing in barrels.
The decisive factor may also be the fact that the pretreatment with alkaline cyanide processes must be less intense than with acidic ones. In certain cases, zinc layers of alkaline electrolytes can be better passivated, sometimes better degasified to drive off hydrogen.
Often the alkaline character is necessary because of the base material, but it may also be that the conversion of a system is too complex or integration into a process sequence does not allow acidic solutions.
In such cases it is then necessary to look for an optimum solution for the problem from the range of alkaline electrolytes. usually cyanide or cyanide-free electrolyte are worth considering.
1.1 Electrolytes with Different Cyanide Content
Alkaline cyanide electrolytes are very variable and can be applied in almost any concentration to obtain different properties. However, a requirement for the function is that the components of the electrolyte always have a certain relationship to each other.
Especially important are the ratios of zinc to cyanide and ratios of zinc to hydroxide, which means the values of the quotients. The quotient MCN influences the temperature sensitivity and depth dispersion of the seperation.
The quotient MOH is important for the anode solubility and the electrical conductivity of the electrolyte, which means the amount of the applicable current density.
The variability of the cyanide electrolytes also makes it possible to lower the cyanide content in order to obtain reduced wastewater treatment costs through reduced cyanide carryover.
This advantage is achieved, in particular, by the fact that, with the lower cyanide concentrations, the cyanide contents sink into the rinses or the service life of stationary rinses increases.
However, it is not always possible, or only to a limited extent, to adjust the concentrations of the other bath constituents in such a way that the optimal conditions are achieved, so that in most cases certain limitations must be expected.
If these are accepted, it is possible to continue with cyanide baths and possibly avoid changing to another process which costs more (other system design, rack system, etc.).
Often the system, ancillary equipment, analytical monitoring, control system, etc. must not be changed at all or should only be slightly changed and above all one can continue relying on existing operating experiences.
As already shown in Table 1, one can choose between:
• High cyanide electrolytes,
• Average cyanide electrolytes,
• Low cyanide electrolytes and
• Low cyanide electrolytes.
The decision, which of these electrolytes can be used without jeopardizing the quality and economy, is individual and depends exclusively on the specific task. The best way to do this depends on the existing electrolyte, which means high cyanide and comparing it with the low cyanide versions.
This results in which bath or layer properties possibly restrictions are possible and how they relate to the expected benefits. The high cyanide is the most robust and variable electrolyte. It will be used wherever good metal distribution at high power is required.
The high cyanide electrolyte allows the application of high current densities with a wide optimal current density range, good metal distribution and gloss depth dispersion. The temperature sensitivity is very low, as well as the maintenance and analysis costs.
The disadvantages are the high concentrations of the electrolyte components and the high active ingredient discharge. A medium-cyanide electrolyte is in principle a 1: 1 dilution and a highcyanide mixture; it is the most common used one in the practice.
If there are no extreme demands on the depth dispersion and a bit more effort is put into it, it can always replace the high cyanide electrolyte.
The maximum current densities, the current density range, the metal distribution and the depth of gloss distribution are quite comparable with the high-cyanide, taking into account the lower temperature sensitivity of the average-cyanide electrolyte.
Therefore the temperature must be kept constant within a narrower range. Also, the electrolyte is more sensitive to a change in the concentration ratios of the bath constituents than the high-cyanide, which means the maintenance and analysis effort is higher.
The advantage is that in the medium-cyanide electrolyte usually the same brightener additives are used as in the high-cyanide, the degree of gloss is sometimes higher.
When low-cyanide electrolyte is used, a lower maximum current density, a smaller current density range, lower gloss depth dispersion and poorer metal distribution is to be expected.
The electrolyte is mainly used when simpler parts are galvanized, no special requirements are needed for the layers, the deposition rate is secondary and the saving of chemicals is a priority. Compared to the high cyanide electrolyte, about 30% of the chemical costs can be saved.
However, the low-cyanide electrolyte needs other brighteners and some of them may be more expensive. The cyanide-poor electrolyte is actually a compromise solution in case that cyanide-free electrolytes can not be used for some reason.
Because of the low applicable current densities, these electrolytes are mainly used for barrel galvanizing. Their main advantage is based on low cost of care, maintenance and detoxification.
Compared to the high-cyanide electrolyte can be saved up to 90% of chemical costs, but is usually expected to incur higher costs for the required brightener additives. Comparisons of the power performance and economic efficiency of the individual electrolytes can be found in the data in Table 3.
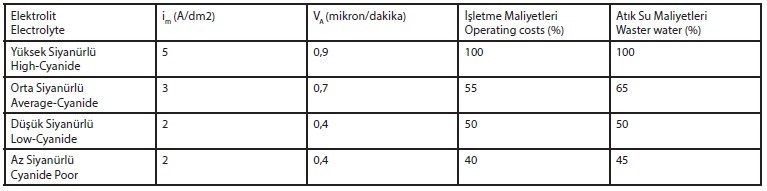
Table 3: Power performance (average current density im, average separation rate VA) and economic efficiency (relative operating and wastewater treatment costs) of cyanide electrolytes of different concentration
For the case that an existing electrolyte is to be converted to a low-cyanide, of course, lower costs are to be expected. Especially when it comes to larger electrolyte volumes and if the conversion should take place without interruption, it can take depending on the throughput a time of weeks or even months.
Since the quality also has to be maintained in the meantime, a greater analytical effort can be expected. So there will definitely be situations, where a new approach could be more cost-effective.
1.2 Alkaline Cyanide-Free Electrolyte
Zinc seperation from alkaline cyanide-free electrolytes, which consists of hydroxo complexes of zinc, distinguishes two types of operationally applicable processes. In addition to brighteners, conventional zinc baths also require so-called soft chelating agents for the seperation of compact layers as an additive.
Although they can only be used to a limited extent on an operational scale because the electrolyte composition and working parameters must be kept constant in very narrow ranges for a satisfactory seperation.
As far as they are still used today because of their good opacity, the application is limited to galvanics with a fixed program and without a variety of parts. A change from cyanidic electrolytes to such a group is generally out of the question.
The new generation of electrolytes, which are known for several years now, is based on the addition of synthetic polymers that modify the cathode reaction.
Since they also allow the use of more concentrated electrolytes (14 to 26 g / l of zinc and 105 to 165 g / l of sodium hydroxide compared to the data in Table 2), high-gloss layers can be seperated with good depth dispersion in a relatively wide range of current density at a good rate.
The electrolytes have a good opacity and the layers are sufficiently ductile. Therefore, electrolytes of the new generation are quite suitable to replace cyanide electrolytes with avarage requirements.
For the conversion, the cyanide is processed to the cyanidepoor electrolyte. Under constant control, it is possible to switch to cyanide-free operation by adding the appropriate additives.
The time period, until the rinsing water ist cyanidefree, so that no more cyanide poisoning in the wastewater must be carried out, is problem-dependent and can last very long. For this reason, it is in most cases easier, safer and significantly less expensive to set a new one.
2. Quality Assurance During Galvanizing (Zinc Plating)
Quality assurance in electroplating has a special significance. First of all because faulty layers, especially in functional applications, can have exceptionally far-reaching consequences. On the other hand, it is also a prerequisite for cost-efficient and environmentally friendly operation.
The most important criteria for the evaluation is also the avoidance of faulty layers in order to avoid the high cost of stripping and re-coating. The avoidance of faulty seperations involves a series of technical and organizational measures to comply with all the parameters that influence the separation.
What these measures are and how they should be applied and controlled is today known through many standards and a comprehensive monitoring system.
While the quality assurance measures are intended to achieve the separation of defect-free layers, quality control checks whether the deposits made comply with the specified requirements.
However, the reproducible quality is only guaranteed once the feedback between quality control and quality assurance measures have been implemented.
In galvanic operations, the most important technical quality assurance measures consist of monitoring and maintaining the electrolyte composition and controlling the seperation conditions (current density, temperature, bath movement, etc.).
The quality control, on the other hand, essentially involves checking the electrolyte properties (scattering, current density range, gloss, etc.) using, for example, the Hull cell test and the relevant layer properties such as layer thickness, gloss or hardness.
To effectively ensure a reproducible quality, it is necessary to establish correlations between the electrolyte or layer properties on one hand and the electrolyte composition or the deposition parameters on the other hand.
Such correlations have been studied for most methods and are published in the literature in the form of so-called error tables or made available by the process suppliers. In the practice of galvanic operations, such tables, together with information on the operating conditions of the electrolytes, are essentially used to quantify the quality assurance measures.
For example, to determine within which limits the temperature may fluctuate, after which throughput gloss additives must be dosed etc. An automatic feedback, for example, the control of the exposure time or current density on measured layer thickness values, can only be found in rare cases.
This is actually an implementation of the relationships contained in the tables, but is one of the main objectives of the technology, especially in the functional electroplating.
İzzet Aydın - Genel Müdür / General Manager - Hillebrand Chemicals Kimyasal Pazarlama Ltd. Şti