Fast Quality Control in Polyurethane Production:
Hydroxyl Number in Polyols and Isocyanate Content in Polyurethane Under 1 Minute with Vis-NIRS
Introduction
Plastics and polymers have become an integral part of today’s modern lifestyle. They can be converted into almost any shape, depending on their physical structure, the variable parameters they contain, and the different degrees of flexibility they have.
The production processes of plastics can vary according to their intended use, and today they can be found in a wide range of products ranging from airplane and car parts to packaging, medical device products and textiles (and even to many other vital components to sustain our life).
Polymer production is a demanding process where high purity raw materials undergo complex reactions and are converted into polymers, fibers, resins, and rubber. To ensure that these products meet expected specifications, quality control analyses must be applied, from raw material input to reaction management, from intermediate product optimization to final product quality and even energy consumption, recycling, and sustainability.
Considering the consumption rate and the importance of product quality, it is of great importance for the manufacturer to perform quality control analyses meticulously, accurately, quickly and at low cost.
Polyurethanes (PU)
Polyurethanes (PU) were invented in 1937 by the German chemist Dr. Otto Bayer (1902–1982), and come up as a subclass of polymers. During World War II, the use of
polyurethanes became popular, replacing then expensive and difficult to obtain rubber, and in the 1950s they began to be used in adhesives, elastomers, rigid foams, and flexible cushioning foams.
Today, polyurethanes can be found in unlimited number of forms and can be used in a wide variety of everyday products, ranging from coatings and adhesives to shoe soles, mattresses and foam insulation.
[caption id="attachment_152645" align="aligncenter" width="393"]
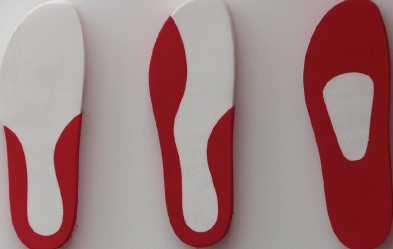
Figure 1: Polyurethane in soles of shoes[/caption]
Polyurethanes are obtained by reacting polyols (namely, alcohols containing more than two reactive hydroxyl groups per molecule) with di-isocyanates or polymeric isocyanates. Appro-priate catalysts and additives may also be used, if necessary.
Since both various di-isocyanates and a wide variety of polyols can be used to produce polyurethane, a wide range of poly-urethane materials can be produced to meet specific requirements for different applications. Polyurethanes can be found in a variety of forms, including rigid foams, flexible foams, specialty adhesives, chemical resistant coatings, sealants, shoe soles, sealants, and elastomers.
The properties of polyurethanes are highly dependent on their production process. When the polyol chain is long and flexible, the final product will be soft and elastic. On the other hand, if the extent of cross-linking is very high, the final polyurethane product will be tough
and rigid.
The cross-linked structure of polyurethanes generally consists of three-dimensional networks which result in very high molecular weights. This structure also accounts for the thermosetting nature of the polymer since polyurethane typically does not soften or melt when exposed to heat.
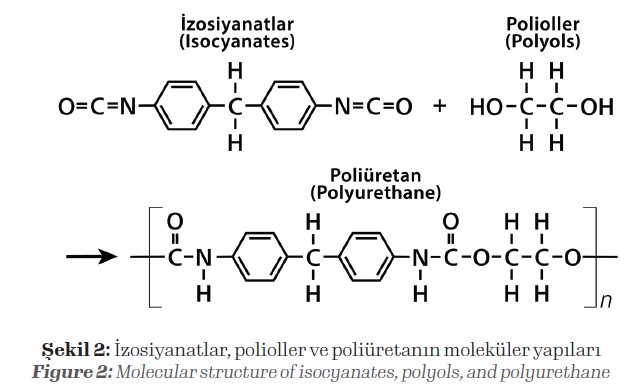
One of the most popular forms of polyurethane is foam (rigid and flexible). This form is obtained by facilitating the production of carbon dioxide gas during the urethane polymerization process.
The properties of polyurethanes are typically comparable to other conventional materials such as rubber, metals and plastics.
Various standard analytical techniques and methodologies are used for the parameters monitored in the polyurethane raw material and quality control processes; Titrimetric techniques for hydroxyl number measurements in polyols, HPLC analyses for NCO
(isocyanate) measure-ments in polyurethane, and Karl Fischer titration for moisture determination stand out as the leading ones.
In addition to the fact that most of these techniques require long and difficult sample
preparation stages, potential errors that may occur in these processes can cause significant delays in the production stages and financial losses on the basis of total turnover due to faulty production.
In this review article, we aim to examine some of the analyses performed during raw material and quality control in polyurethane production and provide detailed information about the advantages Near Infrared Spectroscopy (NIRS) techniques can provide to these
processes.
Near Infrared Spectroscopy (NIRS)
Near Infrared Spectroscopy (NIRS) is a technique built on a principle based on the interaction of molecule and light. Compared to traditional methods in quality control
analyses, it makes important contributions to the practical, fast and precise tracking of critical parameters.
In addition to being a non-destructive method, the NIRS technique does not require any sample preparation, allowing one to perform faster, more environmentally friendly, and cheaper analyses compared to wet chemistry methods.
The NIR spectrometer measures the interaction between light and matter to create a spectrum. Near Infrared Spectroscopy is particularly sensitive to the presence of certain functional groups such as -CH, -NH, -OH and -SH.
This makes NIR Spectroscopy an ideal method for the measurement of many chemical parameters such as water content (moisture), hydroxyl number, NCO. In addition to chemical parameters, since the interaction between matter and light also depends on the matrix of the sample, it is also possible to determine the physical and rheological parameters of polymers.
Near Infrared Spectroscopy (NIRS) has been an established method for both fast and reliable quality control within the polyurethane industry for more than 30 years.
Quality Control Points with NIRS in the PU Production Chain
Quality control analyses of PU are important and necessary in many specific steps of the process, from the production of pure polymers to the processed finished product form. Operational steps from raw plastic producer to plastic parts producers, with some optional steps in the production chain (additives), are typically as follows:
The first step in which near infrared laboratory devices can be used is where raw material (polyol, isocyanate) qualities are verified and pure polymers such as PU are produced. NIRS is also a quite important and very useful technique in the process where polymers are compounded with additives to form intermediate products to be used in subsequent steps.

Typically, a plastic part manufacturer with an extrusion, injection molding or film blowing process evaluates the quality of the received polymer batch to ensure efficient production. In many cases, the certificate from the supplier is trusted without verification.
On the other hand, the rapid increase in the number of companies producing for the medical industry or producing parts at high cost and large quantities brought about the need for monitoring of important rheological quality parameters of each polymer batch before use in injection molding, extrusion or film blowing processes.
Feeding an out-of-spec polymer to the manufacturing process results in costly equipment downtime as well as time-consuming cleaning processes. A quick pre-check of the starting polymer materials used in the process is an ideal solution to avoid such risks and possible loss of time.
In this context, NIRS stands out with its high speed, low operating costs and the ability to be used by personnel who do not have detailed chemistry knowledge. Quality control analyses can also be performed using NIRS, when the final part is created at the end of the production process.
During the production of different types of polyurethane, it is very important to control certain parameters in order to guarantee a quality product output. These quality parameters typically include hydroxyl number, acid number, water content and color for polyols, NCO (isocyanate) content, moisture content and acid number for polyurethanes.
Determining the parameters listed in Table 2 can involve long and tough processes with traditional laboratory techniques, due to the need to use different analytical methods for measurement and various accompanying measuring equipment.

With Metrohm’s new Polyol Analyzer system, which combines the visible (Vis) and near infrared regions (NIR), the nondestructive and chemical-free measurements of a variety of quality control parameters, both chemical and physical, can be done in less than a minute
without any sample preparation and the need for consumables by using techniques developed in accordance with ASTM E1655-17 NIRS application guidelines.
Experimental Content and Workflow
In this review, repeated measurements were performed in transmission mode for analyses of hydroxyl number in polyol samples and isocyanate content in polyurethane samples, covering the entire Vis-NIR wavelength range (400-2500 nm) using a Metrohm DS2500 Polyol Analyzer.
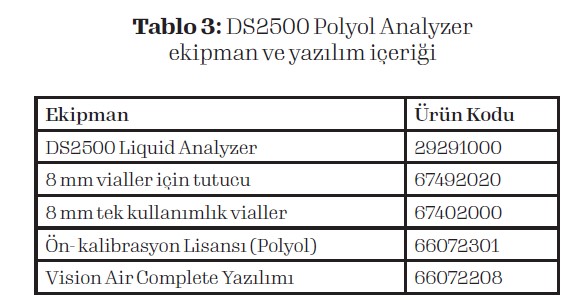
Repeatable spectra were obtained by placing all polyol samples in 8 mm disposable vials at a constant temperature of 30°C using the integrated temperature control of the DS2500 Polyol Analyzer. As can be seen in Figure 5, all measurements were carried out without any preliminary sample preparation.
Method Development
Vision Air Complete software package was used for data collection, model creation and quantification method development processes.
Thanks to this triple package software, which takes the user interface experience to a totally new level, whil all instrument management, including the assignment of operation procedures, was carried out from within the office with the help of the Vision Air Manager Network, all actual measurements were carried out with the Vision Air Routine interface
in the quality control laboratory.
Obtained spectra were automatically uploaded to the database and made accessible
for method development. Quantitative method development was done on Vision Chemometry Software.
Analysis Results
The obtained Vis-NIR spectra (see Figure 6 and Figure 7) were used to generate prediction models to be used for quantitative determinations of hydroxyl number in polyol samples and isocyanate content in polyurethane samples.
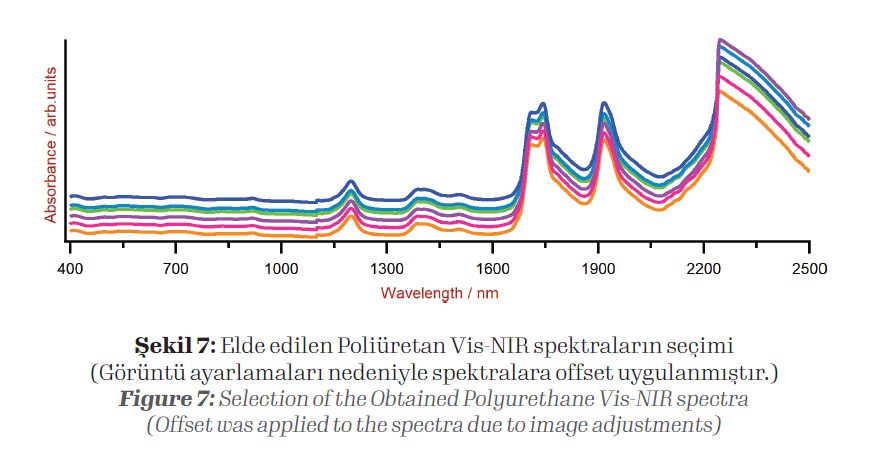
The quality of the prediction models was evaluated within the correlation graphs that show the relationship between values from laboratory primary methods and Vis-NIR data (see Figure 8 and Figure 9). Figures of Merit (FOM) regarding expected data accuracy during
routine analysis are also shown in these figures.
Conclusion
This review shows that it is possible to perform Hydroxyl number analyzes in polyol samples using the Nearinfrared Spectroscopy (NIRS) technique in accordance with ASTM D6342-12. The NIRS technique also allows high-speed determinations of isocyanate content in polyurethane samples.
Compared to wet chemistry methods, fast and simultaneous analyses reveal the most striking advantage of the NIRS technique. Particularly, the fact that hydroxyl number can be determined in less than one minute and without using dangerous chemicals, contrary to the methodology applied in the ASTM D4274-16 directive, enables superior time, high occupational safety, and cost savings, especially in the polymer and chemical industry.
Kaynaklar
1. Metrohm Blog, NIR Spectroscopy in the polymer industry: The ideal tool for QC and product
screening – Part 1
2. Metrohm Blog, NIR Spectroscopy in the polymer industry: The ideal tool for QC and product
screening – Part 5
3. Metrohm Uygulama Notu, AN-NIR-035 Quality Control of Polyols
4. Metrohm Uygulama Notu, AN-NIR-068 Quality Control of Isocyanates
5. Metrohm Broşür, 80005287EN Polymer and plastics analysis – Quality control for polymer
production
6. Metrohm White Paper, WP-036 Lean manufacturing of polyurethane, assisted by near-infrared
(NIR) and Raman spectroscopy
Yeliz Yavuz Çevik
Product Manager Electrochemistry / Spectroscopy
Metrohm Turkey