EVA Equivalent Polyurethane Slipper and Sneaker Systems
Footwear users prioritize comfort and durability, and when choosing, they make their choices on shoes that provide these features. Besides the customers, shoe sole producers are also familiar with this concept. With EVA equivalent slippers and sole systems developed by Flokser Kimya, it aims to solve the need in the sector, which combines these features.
Slipper and sneaker products produced with EVA (ethylene vinyl acetate) provide comfort to users with their lightness and soft structure. However, EVA cannot be used standalone due to its bad mechanical performance and short product lifecycle. Therefore, this disadvantage forced manufacturers to hard polyurethane system with high density and better mechanical properties which cannot achieve the desired level of comfort by EVA. The applications made in the sector represent two extremes with the basic features provided by these two different raw materials.
Soft slipper systems of
Flokser Kimya, which was one of the product group shaped the market in the past, were highly appreciated by the users and led to the emergence of different needs. Therefore, Flokser Kimya R&D center found a solution for this dilemma
and brought the two extreme properties provided by EVA and polyurethane together in polyurethane and presented it to the market. There is no similar polyurethane in the sector yet.
EVA equivalent polyurethane systems are developed for both slipper and sneaker applications.
The standard polyurethane systems used in the production of slippers have a density of 250-300 kg/m3 with hardness in the range of 45-60 shoreA. The EVA equivalent slipper systems, on the other hand, enable the production of soft slippers with 20-25 shoreA
hardness, which provides comfort and convenience with the same density to the user, instead of the 45-55 shoreA hardness of standard slipper products. Since the slipper has this hardness and its in-mold flowability are better than standard slippers, it also enables the production of closed slippers that do not require mattresses and uppers. In addition, in designs that require insole application, it is preferred over insole applications with polyether polyol content, for its softness.
[caption id="attachment_134121" align="aligncenter" width="506"]
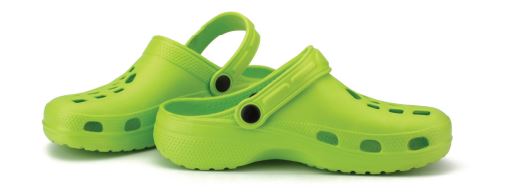
Figure 1. Textile-free PU slippers.[/caption]
The standard polyurethane systems used in sneaker production have a density of 350-450 kg/m3 with hardness in the range of 40-50 shoreA. In addition, in the flex test, which is one of the tests that shows the durability of the product depending on use, a result in the range of 80,000 - 100,000 steps is obtained at -5°C. The developed EVA equivalent sneakers product allows products with the same hardness of 280-350 kg/m3 density. Our EVA equivalent polyurethane sole product provides a weight advantage of approximately 25%.
Compression set test, according to ASTM D395 test standard, is a test method which measures the shape recovery capability of shoe sole under load. In compression set, EVA shoe sole recovers 10% of its original shape, while our developed H-510 and H-466 product can recover about 74% of its original shape after load. Besides, it does not require the use of a secondary material like in EVA. Thus, it also provides an operational advantage. In addition our EVA equivalent polyurethane product provides a better abrasion resistance by losing 25% less relative volume in the abrasion test compared to EVA.
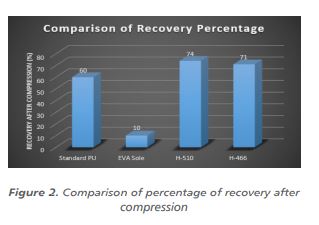
EVA equivalent polyurethane slipper and sneaker systems harmonizes cost effectiveness and comfort in every step of your life.
[caption id="attachment_134123" align="aligncenter" width="628"]
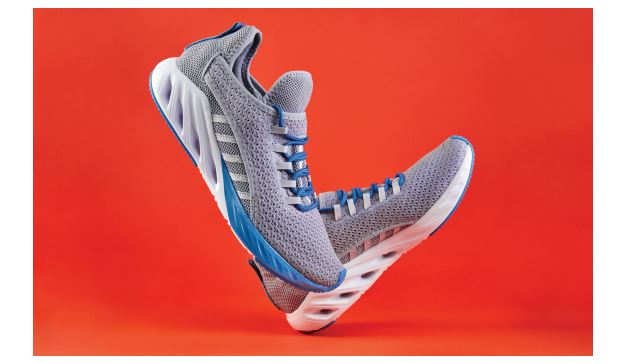
Figure 3. Low density sneaker.[/caption]
The comparison of our EVA equivalent polyurethane system with standard slippers and sole properties is shown in Table 1.
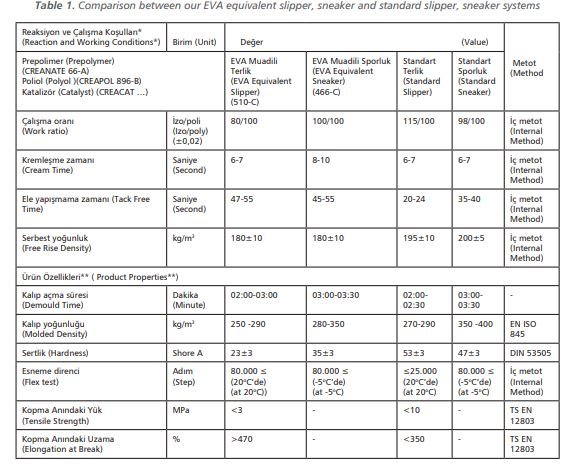
* The reaction and working conditions were obtained as a result of measurements made with a low pressure casting machine operating at 6000rpm.
** According to TS EN 12222 standard, test results of the samples were given after conditioning at 23±2 temperature and 50% relative humidity for 24 hours.
Dr. Serpil Yılmaztürk Güney
P&D Manager
Flokser Kimya
Kerim Can Ünlü
P&D Executive
Flokser Kimya
Tibet Hüten
P&D Researcher
Flokser Kimya