Ether Bazlı Döküm Poliüretan Hammaddelerinin Karşılaştırılması
Hepimizin yakından bildiği üzere Covid-19 pandemisi ile birlikte dünya bambaşka bir hale büründü. Sağlık tarafında yaşanan sıkıntılara özellikle kimyasal hammaddelerde yaşanan tedarik sıkıntıları, lojistik problemleri gibi sorunlar eklenince kimyasal hammaddelerin
fiyatları çok hızlı şekilde artmaya başladı.
Ether türü polioller, özellikle de PTMEG türü ether polioller fiyatı en hızlı ve en çok artan kimyasallardan biri oldu. Çünkü genel anlamda yaşanan bu sıkıntılara ilave olarak yükselme trendinde olan bazı sektörlerin PTMEG piyasalarını ilgilendiren tedarik zincirinden yüksek miktarda malzeme çekmeye başlaması PTMEG (ve aynı zamanda 1,4 bütandiol) kanadında ciddi tedarik problemlerine ve fiyat artışlarına sebep oldu.
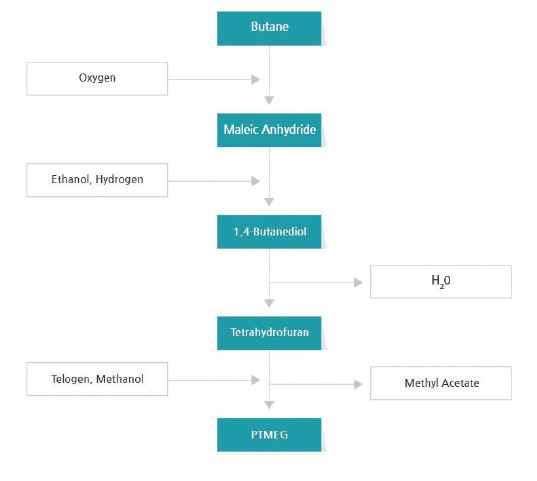
Bu grafik PTMEG’nin üretim aşamalarını göstermektedir. PTMEG, ilk baz malzeme girişinden sonra 4 aşama üretim yapılarak elde edilen, üretimi zor ve zahmetli bir kimyasaldır.
Hızla gelişmekte olan biyoplastik pazarı ve biyoplastik hammaddelerin üretiminde yoğun olarak kullanılan 1,4 bütandiol öncelikli olarak bu sektöre satılmaya başlamıştır. Yüksek miktardaki talep, daha yüksek kar marjı 1,4 bütandiol için biyoplastik sektörünü öncelikli hale getirmiş, 2 aşama üretim yapılarak elde edilen 1,4 bütandiol, daha fazla kar getirince 4 aşama üretimle elde edilen PTMEG geri plana itilmeye başlamıştır.
PTMEG üretmek için yeterli 1,4 bütandiol kalmayınca ve PTMEG üretim miktarları düşmeye, üretim maliyetleri de artmaya başlayınca kısıtlı tedarik ve artan üretim maliyetleri PTMEG
fiyatlarının çok hızlı yükselmesine sebep olmuştur.
Pandeminin ve getirdiği sıkıntıların devam ettiği bu süreçte, ilave olarak poliüretan ve biyoplastik sektörlerine yeterli 1,4 bütandiol kapasitesinin olmaması PTMEG fiyatlarını daha da artıracak gibi görünmektedir. Bu problem de döküm poliüretan hammaddeleri ve özellikle ether bazlı hammaddeler kullanan üreticiler için büyük güçlükler yaratmaktadır.
Birçok firma PTMEG bazlı hammaddelerin alternatifleri konusunda araştırmalar yapmakta ve en yaygın eğlimler, PTMEG yerine PTMEG - PPG karışımı polioller ile ya da sadece PPG türü polioller kullanılarak üretilmiş hammaddeleri kullanmak yönünde gelişmektedir.
Sıcak döküm poliüretan hammaddeleri kullanarak çalışan firmaların en çok tükettiği hammadde gruplarından birisi ether bazlı hammaddelerdir. Bu hammadde grubu genellikle düşük viskozite özellikleri göstermeleri ve uzun pota ömrüne sahip olmaları gibi özelliklerle ön plana çıkarlar.
Bu karakterleri sebebiyle de karmaşık yapılı ve büyük ebatlı parçaların dökümünde tercih edilirler. Geçmişte sadece TDI ve MDI türü aromatik izosiyanatlar kullanılarak üretilen ether bazlı poliüretan döküm hammaddeleri varken sonraki dönemlerde HDI ve PpDI gibi alifatik izosiyanatlar kullanılarak da üretilemeye başlandı.
Her izosiyanat türünün ether bazlı bu hammaddelere kattığı karakteristik özellikler olsa da bu yazıda ether poliol türlerinden yola çıkarak TDI türü izosiyanatlar kullanılarak üretilen ether bazlı hammaddeleri birbirleri ile kıyaslayacağız.
Genel olarak döküm poliüretan hammaddesi üretmekte kullanılan iki tür ether poliol vardır. İlki, kısa adı PTMEG bir kimyasal olup bu poliol kullanılarak üretilen döküm poliüretan hammaddeleri de üst sınıf hammaddelerdir.
Dayanıklılık, kullanım ömrü ve performans tarafında diğer poliol türü olan PPG’den çok daha iyi sonuçlar elde edilmesini sağlarlar. Kısa adı PPG olan polipropilen glikol türü polioller kullanılarak üretilen döküm poliüretan hammaddeleri özellikle kesme-yırtılma dayanımı
ve aşınma direnci çok zayıf olan ürünler elde edilmesine sebep olurlar.
Aşağıdaki tabloda, TDI türü izosiyanat kullanılarak üretilmiş 3 farklı ether bazlı döküm poliüretan hammaddesi kıyaslanmaktadır. Bu hammaddlerin ortak özellikleri, TDI ether grubu hammaddeler olmaları ve MOCA türü kürleştiriciler kullanılarak dökümleri yapıldığında 90 ShA sertlik elde edilmesini sağlamalarıdır.
• A olarak bahsedilen hammadde, TDI + PTMEG ether türü poliol ile,
• B olarak bahsedilen hammadde, TDI + PTMEG – PPG ether poliollerinin karışımı ile,
• C olarak bahsedilen hammadde, TDI + PPG ether türü poliol ile üretilmiş hammaddedir.
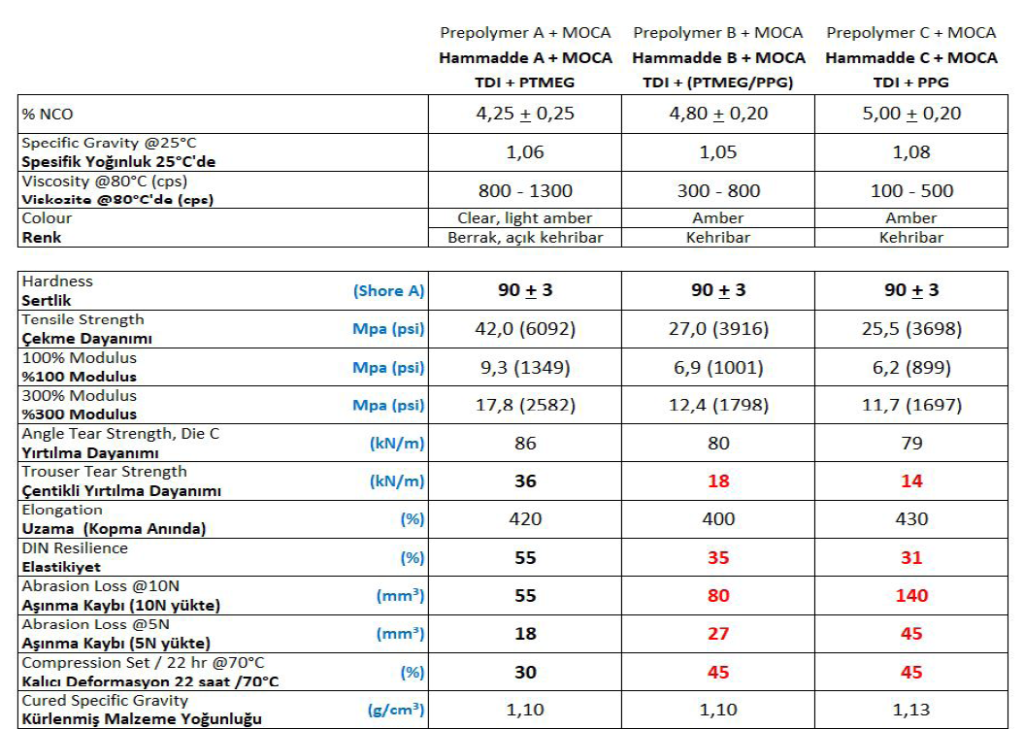
Tablodaki değerlerden de görüleceği üzere, içerikteki PTMEG miktarı azalıp PPG miktarı arttıkça, döküm poliüretan hammaddesinin neredeyse tüm dayanım özellikleri
dramatik şekilde düşüş gösterir.
Örnek vermek gerekirse, TDI + PTMEG esaslı hammadde kullanan üreticinin sıyırıcısı uzun süre aşınmadan çalışabilirken TDI + PPG esaslı hammadde kullanan üreticinin sıyırıcısı adeta bir “kırtasiye silgisi” gibi gördüğü her sürtünme etkisinde eriyecek gibi hızlı bir şekilde aşınma kaybına uğrar.
Aynı şekilde, maden elekleri üreten firmaların elekleri ve o eleklerin sahadaki aşınma miktarları hammaddenin poliol türüne göre ciddi oranda değişim gösterir. Transpalet tekerleri, forklift tekerleri ya da ağır yük tekerleri için de durum benzerdir.
Kalıcı deformasyon ve elastikiyet değerleri PTMEG bazlı hammaddelerin bu uygulamalara en uygun yapıda olduğunu, tamamen PPG bazlı hammaddelerinse bu uygulamalara hiç de
uygun olmadığını gösterir.
Benzer durumlar beton püskürtme nozulları, kaya kırıcılarının darbe takozları ya da
vibrasyon kazanlarının iç kaplamaları için de geçerlidir. PTMEG / PPG karışımı kullanılarak üretilen hammaddelerden alınacak verim de PTMEG bazlı olan tipten uzak ve PPG bazlı olana yakın olacaktır.
Çünkü PPG poliolün zayıf mekanik özellikleri karışım yapılsa dahi performansı önemli ölçüde geriletmeye yetecektir.Üreticilerin bu 3 farklı hammadde türünü tespit etmekte kullanacağı en önemli yöntem hammaddelerin NCO seviyelerini kıyaslamaktır. Aynı sertlik değerinde hammaddeler için konuşursak;
• İçerikteki PTMEG miktarı ne kadar çoksa ya da içerikte PPG yoksa en düşük NCO seviyesi ile o sertlik değeri yakalanır. (Tabloda, 90 ShA sertlik için NCO değeri ortalama 4,25’tir)
• İçerikteki PPG miktarı ne kadar çoksa ya da içerikte PTMEG yoksa en yüksek NCO seviyesi ile o sertlik değeri yakalanır. (Tabloda, 90 ShA sertlik için NCO değeri ortalama 5,00’tir)
Tablodaki değerlerden ve yukarıdaki açıklamalardan da anlaşılacağı üzere, PPG bazlı ya da PTMEG/PPG karışımlıTDI ether hammaddeler kullanmak üreticilere maliyet avantajı dışında başka hiç bir artı özellik sağlamaz.
O yüzden performansın ve çalışma ortamındaki dayanıklılığın önemli olduğu yerlerde ether bazlı bir hammadde kullanılacaksa tercih PTMEG bazlı olan hammaddeden yana kullanılmalıdır.
Serkan İltan
Kauçuk & PU Satış Müdürü
Veser Kimyevi Maddeler A.Ş.