Effects of Extenders Ratio in Heat Resistance Paint Formulation
As the human population increases, new necessities are born. Our expectations from every day items, vehicles, and tools increase as the technology advances over time. From esidential ovens, grills, industrial chimneys to machine parts, etc., heat resistance has become an important feature.
The consumption of heat resistant paints has been rapidly increasing globally. In general,
heat resistant paints are expected to resist temperatures in between 300-800ºC. Also, they are recommended to be applied as 30-50 µ dry film thickness. Heat resistance is a feature implemented to the paint by its binder. Organic resins are decomposed when they are exposed to high temperatures.
Through Si-O-Si bonds thermal stability, silicone resins are highly heat resistant compared
to the other types of resins. Due to this feature, silicone resins are used in heat resistant paint formulations.
Heat resistant silicone resins are composed of siloxane (Si-O) cage structure, silicate SiO2, or silsesquixane (R*-SiO3/2) structures [1]. Figure 1. shows the chemical structures of silicone resins. R groups are generally alkyl or aryl groups. Silicone resins are heat and radiation resistant. They are transparent in UV and visible spectrum. When formulated with appropriate pigments and fillers, silicone resins provide high performance of heat resistance.
[caption id="attachment_139548" align="aligncenter" width="216"]
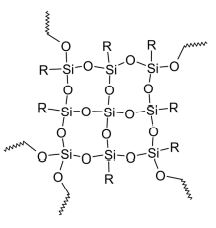
Figure 1. Chemical Structures of Silicone Resins [2].[/caption]Extenders are micron sized solid matters that are obtained through grinding of natural minerals or precipitation of inorganic substances. To decrease the cost of the paint and to improve the physical properties of the paint, extenders are the most commonly used paint ingredient. They play an important role in defining mechanical properties of the paint film. Some examples of extenders and pigments used in heat resistant paints and silicone coatings are titanium dioxide, oxide pigments, spinal pigments, aluminum pigments, mica, talc, barite, and mica-like iron oxide. Extenders we’ve used for our study are listed in the table below.
[caption id="attachment_139549" align="aligncenter" width="618"]
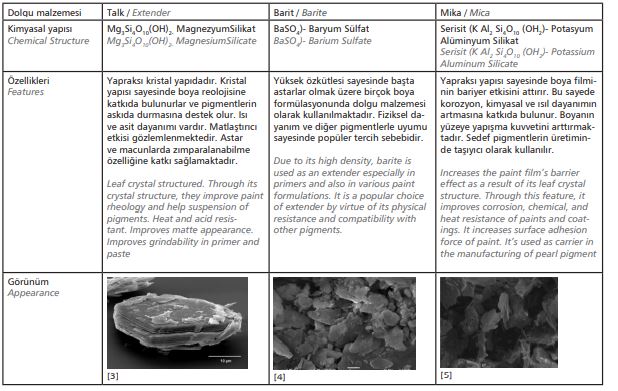
Table 1. Extenders[/caption]
In this study, paints have different extender proportions’ effects on adhesion and heat resistance properties were tested. These paint formulations were designed to have
constant PVC (Pigment Volume Concentration: pigment volume’s ratio to the total non-volatile substance). 6 Sigma methodology was utilized during the experiment design. 2k full factorial experiment design was used. 2 different variants were chosen, film thickness and extender types. Film thickness was set to alternate between 100µ and 200µ. Extender types were determined as barite, talc, and mica. The calculated ratios for 3 different extenders are listed at the table 2 as below. 8 different paint formulations were prepared with respect to extenders. In total, there were 16 different formulation.
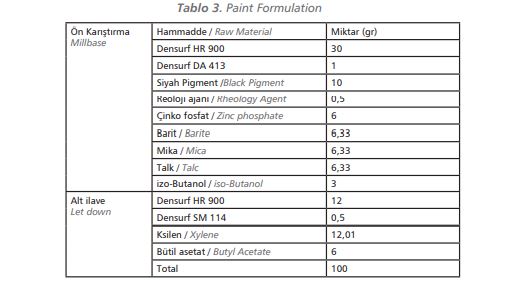
Paint formulations’ particle size of grind was determined as 10-15µ. Prepared paints were applied to metal pannels as 100µ and 200µ wet paint thickness.
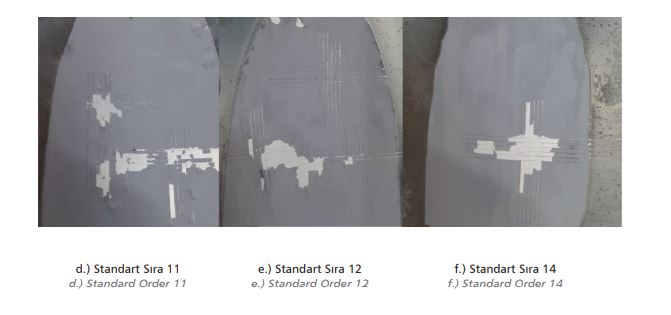
After paints were applied to the pannels, they were cured at 200ºC for 30 minute. After curing process, pannels were held at 600ºC for 2 hours. Last but not least, tests were concluded with the cross cut adhesion test. Pannels with 200µ paints have all shown
unsatisfactory adhesion property after heat resistance test. Pannels with 100µ paints cross cut test results are listed in Figure 2. Study of Standard Order 1’s adhesion performance determined as GT0 according to ISO-2409 (ASTM 3359) standard. This is the best performance result for a paint where there is no deformation.
As a result, heat resistant paint formulation with equal barite, mica, and talc ratio was determined successful. Recommended Densurf products for heat resistant paint systems are listed in the table below.
Note: When conducting a heat resistance study of heat resistant paints, environmental conditions (temperature, humidity, etc.) must be kept constant. Pannels should not be removed from the oven immediately when the test is completed. During the cooldown period, oven should be kept closed until the temperature gets down below 200ºC. Cross cut
test should be performed when pannels reach room temperature.
References
[1]. https://www.yukakimya.com/uploads/docs/boya-egitimi-2021-recineler.pdf
[2]. https://en.wikipedia.org/wiki/Silicone_resin#/media/File:Silicone_resin.svg
[3]. https://mvascientificconsultants.com/sem-analysis-testing-services-lab/talc-particle-electron-microscope-image
[4]. Densification of Concrete using Barite as Fine Aggregate and its Effect on Concrete Mechanical and Radiation Shielding Properties/ Ahmad, Izaz/ Shahzada, / Ahmad, Muhammad Imran/ Khan, Fayaz/ Badrashi, Yasir/ Khan, Sajjad/ Muhammad, Noor/ Jan, Habib/2019/11/21/ Figure.2
[5]. Effect of E-Glass Fibers and Phlogopite Mica on the Mechanical Properties and Dimensional Stability of Rigid PVC Foams/ Jamel, Murtatha/ Khoshnoud, Parisa/ Gunashekar, Subhashini/ Abu-Zahra, Nidal/2015/06/15/Figure 1.
Elif Şentürk
Densurf Application Specialist
Denge Kimya
Hakan Göktürk
Densurf Sales Engineer
Denge Kimya