Mettler Toledo’s new POWERCELL®, technology continuously monitor load cell performance, discovering variances before they impact productivity. This allows manufacturers to stay in control of processes and avoid mistakes before they cost money.
Without the kind of continuous monitoring offered by POWERCELL®, errors such as load cell overload, poor communication between modules, out-of-symmetry errors, and out-of-range temperatures can go unnoticed for long periods. When they do, out-of-specification batches and poor quality product are the result. Significant costs and damage to company reputation can occur.
POWERCELL®- equipped load cells with on-board microprocessors not only alert operators to performance degradation—they also adjust the weighing signal to compensate for environmental changes. This allows POWERCELL®, load cells to provide accurate weighing regardless of the effects of temperature, linearity, hysteresis, and creep. In the unlikely event of load cell failure, POWERCELL®, design also makes individual load cells easy to replace.
Global approvals are standard on POWERCELL® load cells, including OIML, C3, NTEP 5K, OIML C6, and NTEP 10K.
Measurement errors caused by temperature, creep, non-linearity, hysteresis, etc. are compensated digitally in POWERCELL® and allow for better accuracy and tighter tolerances than analog load cells.
1. Types of Load Cell
Analog System Architecture: In an analog system the cables and junction boxes have a significant impact on the very low level signals and the system must be calibrated as a whole. Any change or replacement of parts requires a full recalibration of the system. In addition, system performance is impacted because the small analog signal is susceptible to RFI/EMI and degradation due to moisture.
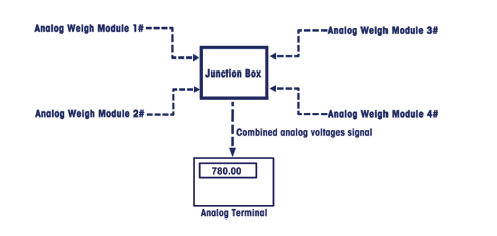
POWERCELL® System Architecture: Obviously such a system has no junction box, thus one significant component less influencing the system performance and reliability. Not so obvious is the fact that the weighing information is provided digitally and hence the cables do not influence the system performance at all. That allows changes or replacement of cables at any time without impacting performance.
2. Performance Differences
Signal Content: Analog systems only provide the combined signal of all load cells. The POWERCELL® network handles the weight information from each load cell separately. Thus the terminal can monitor every load cell individually and can make judgment on load cell and system condition.
Signal Strength: Analog signal strength is very low. Such low signals can be disturbed easily by mobile phones, proximity to large electric motors, moisture,etc. POWERCELL® uses CAN Bus for data transmission. It is a very roboust +/- 5V digital signal commonly used in the car industry. Cable Influence: Analog cables have a significant impact on system performance. Cable length, cross sectional area, quality, shielding,4 versus 6 wire etc. The POWERCELL® system performance is totally independent of the cable influence.
EMI Immunity: EMI immunity is a measure of a system’s ability to withstand influence on it is performance by external electromagnetic fields such as mobile phones, high current lines etc. Analog systems with their low signal strength are very sensitive, POWERCELL® is much more roboust (10V/m field strength system)
Accuracy: A key difference between analog and POWERCELL ® load cells is the method by which the errors inherent to any load cell are compensated. Analog load cells use passive components to compensate temperature effects and to adjust calibration. Passive components are available in a limited range of values thus limiting the precision with which any compensation can be made. POWERCELL® uses the in-built microprocessor and sophisticated sensors and algorithms to compensate performance errors. All of the major sources of error are compensated automatically. First of all higher accuracy is possible even up to the unique OIML class C 10000e performance level which is 3 times higher than standard. Secondly POWERCELL® load cell outputs are matched much more tightly making them 100% interchangeable in the field.
3. Calibration Differences
CalFree™ weightless calibration of larger systems, where calibration with test weights or other means would be impractical, is state of the art. Basically the factory calibration of the load cells is manually transferred to the final system. Analog load cell systems with the uncertain impact of cables, junction boxes and cross talk between cells reduce the transfer accuracy. Additionally the accuracy of the calibration relies on calculations by the technician and means to double check a CalFree™ calibration are limited. In the worst case a completely inappropriate calibration goes unnoticed.
POWERCELL® CalFree™ Plus eliminates many potential sources of failure. Cables have no impact, junction boxes and cross talk effects do not exist and calculations by the technician are not required. Thus the reliability of the calibration with POWERCELL® using CalFree™ Plus is significantly better.
4. Diagnostics and Maintenance Differences
What happens when a signal from an analog load cell is incorrect due to degradation or other reasons? If the error is significant, the scale operator may notice and investigate the cause. However, this would require an experienced operator and be likely only if a load cell was completely “dead”. Otherwise, the scale operator has no way of knowing if the scale is inaccurate. Consequences can be severe, depending on the importance of the equipment to the quality of the final product.
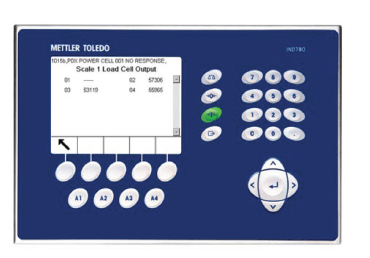
Every POWERCELL® is equipped with sensors that monitor the performance of each cell. Should a problem be imminent, a message is generated at the scale terminal noting the specific cell affected and the issue it is experiencing. The scale can continue to operate normally until the load cell can be replaced at a scheduled time. Monitoring the integrity of each load cell eliminates “hidden” problems that eventually can cause unexpected scale failures.
5. Conclusions
POWERCELL® helps to avoid hidden failures which can lead to significant consequences in the end product quality and associated costs. It allows repairs to be made before a failure actually occurs. It also supports quick recovery as the need of recalibration after service is eliminated. This table summarizes the benefits.
Uğur Tuncer
Industrial Division
Business Area Manager
METTLER TOLEDO Turkey