Birçok önemli endüstriyel kaplama ve boyalar, bileşenler arasındaki kimyasal reaksiyonun bir kaplama filmi oluşturduğu iki veya üç bileşenli ürünlerdir (iki kompanentli 2K ve üç kompanentli 3K olarak adlandırılır). Arzulanan son ürünü oluşturmak için, ayrı olarak paketlenmiş bileşenlerin belirli bir oranda karıştırılması gerekir. Tek tenekedeki malzemelerin kompozisyonları çok farklıdır. Bileşenler, birlikte karıştırıldıklarında kimyasal bir reaksiyona girerler. Bu şekilde koruyucu bir kaplama oluşturan çapraz bağlı bir polimer materyali oluştururlar.
Satın alınan malzeme için ürün bilgi föyü (PDS veya TDS), bileşenlerin doğru karıştırma oranını ve karıştırma parametreleriyle alakalı üreticinin bilgilerini içerir. İki ve üç bileşenli kaplamalar da olsa, bu yazıda öncelikli olarak iki bileşenli malzemeler üzerine odaklanılacaktır çünkü bunlar kaplama endüstrisinde daha yaygın görülmektedir.
Genel olarak, kaplama/boya üreticileri, malzemeleri, her bileşenin doğru miktarını (oranını) içeren önceden ölçülmüş iki tenekede sunmaktadır. Doğru bileşen etiketi ile tanımlanır ve verilen baz miktarı aktive edici miktarı ile karıştırılır. Genellikle bir karıştırma kiti olarak anılan, önceden ölçülen bu ambalaj, ürünün, her bileşenin ayrı ayrı orantılı olarak bulunmasına gerek kalmadan kullanılmasına izin verir. Yine de, önceden ölçülmüş ambalajlamayla bile, bileşenlerin doğru oranlarda karıştırılmadığı durumlar yaşanabilir. Bazı durumlarda, önceden ambalajlanmış bir kitin tek tek bileşenlerinin ölçülmesi ve orantılanması gerekebilir, bunun sebebi, malzemelerin sadece büyük miktarlarda (örneğin 5 galonluk kitler) tedarik edilmesi ve karışım ömrü, tek bir karışımda kullanılabilecek malzeme miktarını sınırlayabilmesidir. Ayrıca, eksiksiz bir kitin kullanılmasını gerektirmeyecek küçük alanların onarımı için tamir programları ve gereksinimler, orantılı hale getirmeyi gerektirebilir. Ancak, kaplama üreticilerin çoğu, ambalajlı bir kit olarak tedarik edilen bir ürüne yönelik bileşenlerin oranlanmasını önermez (ve hatta yasaklanmış olabilir).
Doğru Karışım Oranları
Üretici firma, özellikle de kaplama formülatörü, 2K ürün için kaplama bileşenlerinin doğru karıştırma oranını belirlemektedir. Poliüretan ve epoksiler gibi bazı kaplama türlerinde, karışım oranındaki bazı hafif değişiklikler, performansı negatif bir şekilde etkileyebilir. Otomatik çok komponentli sprey ile yaygın olarak uygulanan hızla sertleşen kaplama ürünleri, genellikle karışım oranı çeşitlerine karşı daha hassastır ve son kaplamanın performans özelliklerini küçük sapmalara bağlı olarak büyük oranda değiştirebilir. Uygun karışım oranında izin verilen değişim, kaplama türüne, formülasyona ve son kullanım özelliklerine bağlıdır.
Doğru karışım oranı, reaksiyona giren iki kaplama bileşeninin kimyasal stokiyometrisi ile alakalıdır. İki bileşen vardır ve her biri, nihai filmi oluşturmak için kimyasal olarak bağlanmaya ihtiyaç duyulan bilinen miktarda kimyasal aktif bölgeye sahiptir. Reaksiyonun optimum bir şekilde meydana gelmesi ve polimerleşmenin gerçekleşmesi için, iki bileşen eşit sayıda kullanılabilir alana sahip olduğunda, kimyasal olarak dengelenir. Bu, tüm reaktiflerin baz ya da aktivatör(ya da sertleştirici) bileşeni eksikliği ya da fazla olmamasıyla tüketildiğini söylemenin başka bir yoludur. Bu optimum kimyasal denge, her zaman bir kısım bazın bir kısım aktivatöre bir karışım oranına, hatta iki kısım bazın bir kısım aktivatöre uygun bir oranına dönüşmemesi anlamına gelebilir.
Bilimsel çalışmalar, karıştırma oranı ne kadar sezgisel olursa, materyallerin uygun şekilde karıştırılma olasılığının da o kadar az olduğunu ortaya koymuştur; ancak, burda insan faktörü göz ardı edilmektedir. Yüksek sıcaklıktaki ortamlarda çalışırken, iki komponentli materyallerin karışım ömrü düşebilir, hatta bazen önemli ölçüde. Sabah güneşinde yapılan bir uygulama ise, kaplamanın karışım ömründe belirgin bir azalma anlamına gelebilir. Hızlı reaksiyon, karışım ömrünün kısalmasına bağlı olarak ciddi miktarda israfa ve maliyete yol açar ve düzgün şekilde karıştırılmış fakat kullanılamayan kaplama malzemesine neden olabilir.
Örneğin, aplikatör, sadece A bileşenini uygulayarak ve B bileşenini atlayarak kalan malzemeyi korumaya çalışsın. B bileşeni nispeten küçük bir kısım olduğu için (karıştırma oranı 20A: 1B idi), sadece daha kalın A bileşeninin kalan miktarının yüzeyi sürekli bir film olarak yeterince kaplaması ve ısının kaplamayı iyileştirmesi beklenir. Fakat, kürlenme süresinin oldukça uzadığı görülecektir. Bu yüzden kaplama yeterince sertleşmemesi sebebiyle kuru film kalınlığı okuması elde edilemez ve sonraki kaplama katmanları uygulanamaz.
Endüksiyon Zamanı Nedir?
Bazı kaplamalar, sertleşme reaksiyonunun verimli ve doğru bir şekilde ilerlemesini sağlamak için bir endüksiyon süresi gerektirir. Endüksiyon süresi, yeni karıştırılmış malzemenin uygulamadan önce beklemeye bırakıldığı bir süredir ve her kaplamada bulunmaz. Uygulama bilgi föyünde bilgi verilir.
Genel Olarak Karıştırma
Tüm kaplamalar reçineler, pigmentler, katkı maddeleri ve çözücüden oluşur. Daha ağır pigmentler genellikle tenekenin dibine çöker ve kullanımdan önce iyice karıştırılarak homojen bir şekilde dağıtılmalıdır. Bazen reçine veya çözücü yüzeye çıkabilir. (sinerez adı verilen bir fenomen). Bu berrak sıvı boya formülünün önemli bir parçasıdır ve asla dökülmemelidir - kullanmadan önce tamamen yeniden karıştırılmalıdır.
2’Li Kaplamaların Karıştırılması İçin Prosedürler
Tek komponentli kaplamaların karıştırılması genellikle düz, elektrikli karıştırıcılar, hazneli karıştırıcılar veya boya çalkalayıcıları kullanılarak yeterli bir şekilde elde edilebilir. 2 kompenentli kaplamaların (özellikle yüksek hacimli katılara sahip olanlar) karıştırılması biraz daha güç gerektirmektedir.
Uygulamadan önce 2’li kaplamaların doğru şekilde karıştırılması, tüm boyama prosesinde önemli bir adımdır. Birçok kaplama hatası yetersiz / yanlış karıştırmaya kadar izlenebilir.
2’li kaplamalar söz konusu olduğunda doğru karıştırma için ek bir neden daha vardır. Standart 2’li kit, Bölüm A ve Bölüm B içerir; bir kısmı reaktif reçineyi içerirken , diğeri sertleştirme maddesi veya ‘sertleştirici’ içerir. [Bazı kitler aslında birden fazla paket içerir; reçine ve sertleştirici paketlerine ek olarak bazen reaktif renk paketleri ve hızlandırıcılar da temin edilmektedir.] Reçinenin sertleştiriciye oranının, uygun şekilde karıştırıldığında ikisi arasında tam reaksiyona ulaşmak için doğru oranda olmasını sağlar. Mikroskobik düzeyde düşünün; her molekülün reaksiyona girmesi için reaktif muadili ile iyice karıştırılması gerekir. Bir elektrikli mikser kullanarak karıştırmanın hızı ve verimliliği, moleküler düzeyde, Kısım A ve Kısım B’nin iyice karıştırılmasını ve reaksiyonun karışım boyunca doğru ve düzgün bir şekilde gerçekleşmesini sağlar.
Karıştırma yeterince kapsamlı değilse, Kısım A veya Kısım B’de fazla miktar bulunabilir, bu da bu alanlarda yanlış karıştırma oranlarına neden olur. Buna bazen ‘orantısız’ karıştırma denir. Oran dışı karıştırma aşağıdakilerden herhangi birine veya tümüne neden olabilir:
• Düzensiz, veri sayfasında belirtilenden daha düşük parlaklık,
• Tutarsız sertlik, çok yumuşak veya çok kırılgan alanlar (ürün türüne bağlı olarak),
• Veri sayfasında belirtilenden önemli ölçüde daha düşük sertlik,
• Delaminasyon gibi kaplama hatası, • Blooming gibi film kusurları,
• Yapışmayan veya kürlenmemiş, reaksiyona girmemiş kaplama.
Oran Karışımının Etkileri
Kaplama malzemesinin iki bileşenini üreticinin belirttiği orandan farklı bir oranda karıştırması, son film özelliklerinde değişiklik görülmesiyle sonuçlanabilir. Kaplama uygulanırken belirgin olmayan bu değişiklikler bazen sadece kaplama işlemi tamamlandıktan sonra görünür hale gelir (Şekil 1). Ancak çoğu zmana oran dışı karıştırma nedeniyle oluşan kusurlar, uygulama sırasında görsel olarak belirgindir (Şekil 2). iki bileşenli materyallerin hepsi için işaret olarak kullanılabilecek, oran dışı karıştırılışın etkisini doğrudan gösterecek tek bir fiziksel özellik yoktur. Bu nedenle, oran dışı bir karışımın tanımlanmasını, gözlemlenen kusurun tek nedeni olarak kabul etmek zordur.
[caption id="attachment_103656" align="aligncenter" width="457"]
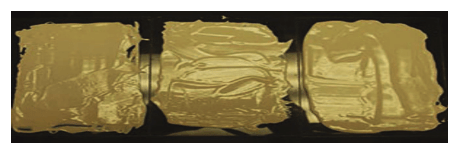
Şekil 1. Aynı maddenin üç karışımı aynı sertlikte parlak yüzeylere tanımlanır. Fotoğraflar KTA-Tator, Incorporated’in izniyle[/caption]
[caption id="attachment_103657" align="aligncenter" width="464"]
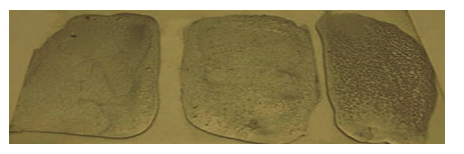
Şekil 2. Aşırı katalize edilmiş malzeme kabarcıklar oluşturarak pürüzlü bir yüzey oluşturur. Köpürme, sağ taraftaki yanlış karıştırma oranında meydana gelmiştir.[/caption]
Kaplama bileşenleri orantısız karıştırıldığında kimyasal reaksiyon dengede değildir ve fazla reaktan varlığı malzemede görsel bir değişikliğe neden olabilir. Kürlenmemiş bir malzemeyi görsel olarak en belirgin ve dokunsal olarak anlatan durum, malzemenin reaksiyona girmemiş ve esasen ıslak kalmış olmasıdır (Şekil 3). Bu, kopmalar, sarkma, ve reaksiyona girmemiş malzemenin yumuşak, bazen yapışkan yüzeyine kir ve döküntünün yapışması anlamına gelmektedir. Anında görsel değişikliğin bir başka örneği, iki bileşenin reaksiyona girmesi ve amaçlanan kaplamadan daha sert bir film oluşturmasıyla hızlı bir şekilde ortaya çıkabilecek çatlamalardır (Şekil 4). Diğer durumlarda, kimyasal reaksiyon tamamlanmasa bile hemen görülebilen bir değişiklik meydana gelmez.
Örneğin, uygun ve oran dışı karışımlar tarafından oluşturulan filmlerin tümü benzer olduğu Şekil 5’ten görünmektedir. Ancak yüzey incelendiğinde, sol taraftaki oran dışı karışımının diğer iki karışıma kıyasla çok daha yumuşak olduğu fark edilmektedir. Görsel çeşitlilikler olsun olmasın, fazla olan bileşenin filmde kaldığını unutmamak önemlidir. Geriye kalan malzeme görünüşte değişikliklere neden olabilir veya olmayabilir. Bazı durumlarda, oran dışı bir karışım ile üretilen film, kaplama türüne ve servis ortamına ve aynı zamanda malzemenin karıştırma oranının derecesine bağlı olarak belli bir zaman boyunca gerçekleşebilir.
[caption id="" align="aligncenter" width="393"]
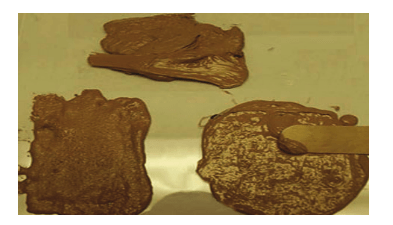
Şekil 3. Sağ taraftaki oran dışı, düşük katalizörlü karışım birkaç ay sonra bile kürlenmedi.[/caption]
[caption id="" align="aligncenter" width="392"]
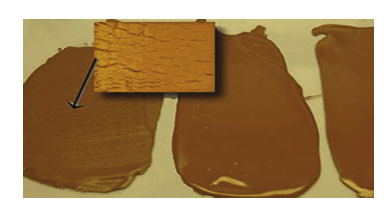
Şekil 4. Sol tarafta düşük oranlı, az katalizörlü karışım çok çatlamıştır. Yerleştirme, 20x’te gösterilir.[/caption]
[caption id="" align="aligncenter" width="351"]
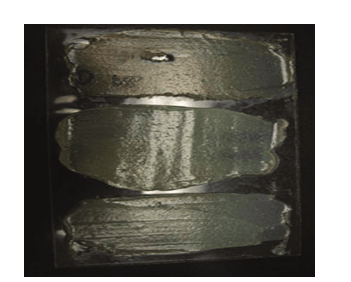
Şekil 5. Parlaklık ve görünüşte benzer olan üç karışımın sertliği farklılaştı.[/caption]
Kaplama Tipine Göre Yanlış Karıştırmalar
Epoksi
Uygun olmayan bir oranda karıştırılmış bir epoksi kaplama, sert ve uygun oranda karıştırılmış bir filmden görsel olarak farklı olmayan bir film oluşturabilir. Bu durumda, karışım dışı oranlı bileşenler tarafından değiştirilebilecek bazı özellikler arasında esneklik, kimyasal direnç, su direnci ve sertlik sayılabilir. Servis ortamına ve orantısız karıştırmadan etkilenen özelliğe bağlı olarak, kusur hemen fark edilmeyebilir. Örneğin, bir beton substrata uygulanan yanlış karıştırılmış bir epoksi, sonuçta ortaya çıkan tek kusur esnekliğin azalması ise, hala substratı koruyabilir.
Bununla birlikte, esnek çelik döşemeye uygulanan aynı yanlış karıştırılmış epoksi kaplama, döşemenin hareket etmesine veya esnemesine neden olan çevre koşullarındaki ilk değişiklikte başarısız olabilir ve nihayetinde delaminasyon yapabilir. Başka bir örnek, ilk uygulandığında iyi görünen epoksi zemin kaplamasıdır (Şekil 6), ancak bina kullanılmaya başlandıktan sonra, kaplama kolayca çizilebilir. Sonunda kaplama esas olarak estetik nedeniyle tamamen değiştirilmek zorunda kalmıştır. Tersine, kimyasal direnç sağlamak için oran dışı epoksi malzeme uygulandıysa, yanlış karıştırılan film, kimyasallara maruz kaldığında yumuşayabilir, rengi bozulabilir veya çözelti haline gelebilir, böylece alttaki substrata kimyasal koruma sağlamaz.
Ek olarak, kaplama kabul edilebilir görünse bile, çözücüler içeren bir üst katın uygulanması, altta yatan bir epoksi orta katını veya astarı zayıflatabilir ve gelecekteki delaminasyona yol açabilir. Uygulanan epoksi amin ile sertleştirilmiş bir malzemeyse, fazla amin, yüzeyde bir amin sızmasına (kızarıklık) yol açabilir, bu da son katın delaminasyonuna neden olabilir.
[caption id="attachment_103661" align="aligncenter" width="594"]
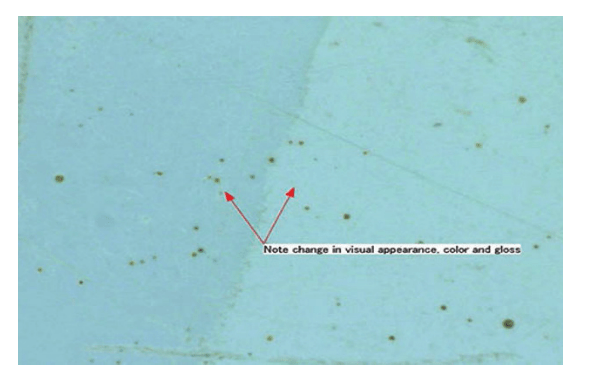
Şekil 6. Oran dışı karışımına bağlı epoksi zemin kaplamanın aşınma direncinin azalması 50x’te görüntülenmektedir.[/caption]
Üretanlar
Uygun oranda karıştırılmamış iki bileşenli üretan malzemeler, renk bozulmasına eğilimli veya parlaklıkta farklılıklar gösterebilen daha yumuşak filmler oluşturma eğilimindedir. Şekil 2, aşırı B bileşeninin kaplamada boşluk ve kabarcıkların oluşumuna neden olduğunu gösterir.
Hemen görülebilen kusurların yanı sıra, güneş radyasyonuyla üretilen enerji, yanlış karıştırılmış üretan reçinesinin erken bozulmasına, renk solmasına ve parlaklığın azalmasına neden olabilir. Bunun yanı sıra, kaplama alt katmana veya altta yatan malzemelere düzgün yapışmayabilir. Üretan malzemeleri formüle etmek için kullanılan bazı hammaddeler suya duyarlı olabilir, bu nedenle bu bileşenlerin tamamlanmamış reaksiyonu, kaplamanın su direnci üzerinde olumsuz etkilere sebep olabilir. Artan su duyarlılığı, düzgün şekilde karıştırılmış üretan kaplamalarının suya erken maruz bırakılması durumunda ortaya çıkabilecek reaksiyonlara benzer şekilde, boşlukların ve su erozyonunun artmasıyla, nihai filmin özelliklerini daha da değiştirebilir.
Poliürealar
Çok çeşitli poliürea reçineleri, poliürea reçinelerinin harmanları ve hibrid formülasyonlar vardır. Bu kaplamaların iki bileşeninin reaksiyon hızının, diğer çok bileşenli kaplamalardan daha hızlı olması, oran dışı karışıma daha duyarlı olmalarına neden olur. Çok fazla formülasyon değişkenleri olduğundan, hem epoksi hem de üretan malzemeler için yukarıda listelenen tüm kusurlar poliürea materyalleri için de geçerlidir. Bu malzemelerin karıştırma oranları büyük ölçüde değişebilir ve bileşenlerin düzgün bir şekilde karışması için uygulama ekipmanının doğru ve düzgün çalışması gerekir. Normalde karıştırma tabanca ucunda gerçekleşir ve saniyeler ile birkaç dakika arasında tamamlanır.
Ürünler buna hızlı tepki verdiğinde, iki bileşenin tamamen tanıtılması ve karıştırılması için daha yüksek bir hassasiyet derecesi bulunur. Oran dışı malzemenin son filmi, reaksiyona girmemiş malzemelerin girdapları ve çizgileri de dahil olmak üzere, yanlış karıştırmanın fiziksel kanıtlarına sahip olabilir (Şekil 7). Diğer durumlarda, malzeme alttaki yüzeye yapışma göstermeyebilir. Diğer kaplama hataları, yapı kullanıma sokulduktan sonra kaydedilebilir. Malzemeler normalde sert, kimyasala dirençli filmleri çok hızlı ürettiğinden, test yapılmadığı sürece yetersiz bir filmin ömrünün ne olduğunun belirlenmesi zor olabilir.
[caption id="" align="aligncenter" width="557"]
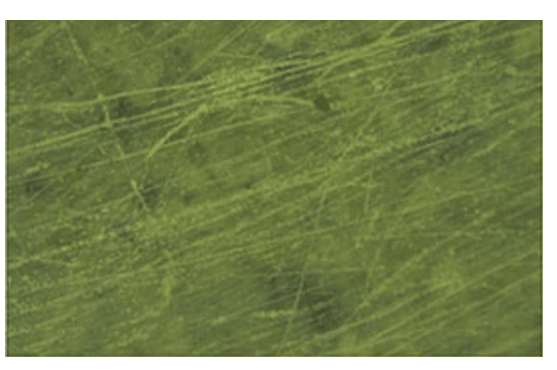
Şekil 7. Çoğul bileşenli malzemenin oran dışı karışımından dolayı renksiz bir kaplama, 20x büyütülmüştür.[/caption]
Karıştırma Oranı Çeşitlerinin İncelenmesi
Solvent Hassasiyeti
Bazı iki bileşenli malzemeleri karıştırma oranı değişimi için incelemenin en hızlı ve en kolay yolu bir solvent sürtünme testidir. Solvent duyarlılığını değerlendirmek için en yaygın yöntem ASTM D5402, Solvent Ovmalarını Kullanarak Organik Kaplamaların Solvent Direncini Değerlendirme Üzerine Standart Uygulamasıdır. Bu yöntem, bir bezin uygun bir çözücü ile doyurulmasını ve kaplamanın yüzeyinin ovulmasını içerir. Çoğu ürün bilgi föyü, bir kaplamanın beklenen solvent direnci değerini listeler. Son film gerekli sayıda çift sürtünmeyi karşılamıyorsa, iki bileşen potansiyel olarak doğru şekilde karıştırılmamıştır. Kaplama tipine ve uygulama ve kürleme koşullarına bağlı olarak bu yöntem, genellikle uygulamadan sonra 12 ila 48 saat içinde gerçekleştirilebilir.
Analitik Yöntemler
Birkaç analitik yöntem, kaplama malzemelerinin uygulandıktan sonra karışım oranını belirlemek için de kullanılabilir. Bu yöntemlerin çoğu, bileşenlerin sıvı kaplama numunelerine ihtiyaç duyar. Bileşenler daha sonra uygun oranda karıştırılır ve aşırı katalizlenmiş ve az katalize edilmiş bir karışımı temsil eden oranlarda tekrar karıştırılır. Kurutulan filmler daha sonra, yanlış karıştırıldığı iddia edilen kaplama malzemesinden ve kontrol numunelerinden elde edilen verileri karşılaştırmak için kullanılabilen 3 noktalı bir veri eğrisini çizmek için analiz edilir. Karışım oranı onayına ulaşmak için laboratuvarda hazırlanan örnekleri kullanabilen çeşitli teknikler vardır. Bu tekniklerden üçü, yani kızılötesi spektroskopi, diferansiyel tarama kalorimetrisi ve azot içeriğini aşağıda inceleyelim.
Kızılötesi Spektroskopi
Kızılötesi spektroskopi ile analiz edilen numuneler, pigment bileşenlerinin iki bileşenden birine özel olması şartıyla, malzemenin reçine ve pigment kısımlarını temsil eden piklerin oranını belirlemek için yorumlanabilen kızılötesi spektrumlar üretir. Ek olarak, reaksiyon bileşenleri ve reaksiyon ürünleri iki bileşenin sertleşmesini takip etmek için de kullanılabilir.
Diferansiyel Tarama Kalorimetrisi
Diferansiyel tarama kalorimetresi (DSC) ile analiz edilen numuneler, malzemenin cam geçiş sıcaklığını tanımlamak için kullanılan veri eğrileri üretir. Cam geçiş sıcaklığı, sertleştirilmiş kaplamanın çapraz bağlanmasından etkilenir. Sertleşmiş bir kaplama ürünü belirli bir cam geçiş sıcaklığı sergilemektedir. İki bileşen doğru oranda karıştırılmazsa cam geçiş sıcaklığı farklı olacaktır. Örneğin, düşük katalizörlü bir malzeme, uygun oranda karıştırılan ürünün çapraz bağ yoğunluğuna ulaşamaz ve daha sonra cam geçiş sıcaklığı beklenenden daha düşük olacaktır. Tersine, aynı malzeme aşırı katalizlendiğinde, çapraz-bağlantı yoğunluğu, uygun şekilde karıştırılmış malzemeden daha büyük olur ve daha yüksek bir cam geçiş sıcaklığına yol açar. Daha yüksek cam geçiş sıcaklığı malzemesi genellikle çatlamaya meyilli olabilecek daha kırılgan bir film ile ilişkilidir.
Azot İçeriği
Azot içeriği için analiz edilen numuneler, bileşenlerden sadece birinin bir azot malzemesi içerdiği kaplama ürünleri ile sınırlıdır. Örneğin, üretan kaplamaların reaksiyona girmemiş izosiyanatı ölçülebilir. Mevcut kontrol numuneleri (doğru oranda karıştırılmış, aşırı katalizli ve düşük katalizli), doğru oranda karıştırılmış üründeki azot miktarının yanı sıra aşırı ve eksik miktarlarda izosiyanat olduğunda azot içeriğindeki değişikliği belirlemek için kullanılır. Azot içeriği, tipik olarak eksik ve fazla miktarda izosiyanat arasında (karıştırma oranına bağlı olarak) doğrusal bir ilişki sergiler. Doğrusal ilişki, aynı teknik kullanılarak test edildiğinde, alana uygulanan kaplamanın karıştırma oranını geri hesaplamak için kullanılabilir.
2 paket karıştırmak için önerilen talimat dizisi:
• Temizleme solventinin mevcut olduğu, uygulamaya başlamadan önce kontrol edilmelidir.
• Bir güç karıştırıcısı ile her bir kabın içindekiler iyice karıştırılmalıdır.
• Kutunun yanlarını ve tabanını gittikçe kazınmalıdır, düz bıçaklı bir bıçak bunu başarmada etkili olabilir.
•Bazların doğru renge boyandığından emin olunmaldır.
• Renk tutarlılığını sağlamak için kullanmadan önce tüm kapların kutulanması gerekir.
• Sabit karıştırma altında bileşenler, önerilen sırada eklenmelidir. Bu genellikle biri dökecek, diğeri karıştıracak iki kişiyi içerir.
• Üreticinin özelliklerine göre bir güç karıştırıcı kullanarak her iki paketin içindekileri iyice karıştırılmalıdır. Tüm ‘Kısım A’ ve ‘Kısım B’ nin karıştığından emin olmak için kabın yanları ve tabanı kazınmalıdır.
Mükemmeliyetçiler genellikle reaksiyona girmemiş malzemenin kontaminasyonunu önlemek için ayrı, temiz bir kaba aktarırlar. Bu takdir edilecek bir hareket de olsa, her iki kabın yanları ve tabanı kazınırsa ve etkili bir şekilde karıştırılırsa, bunun genellikle gereksiz olduğu söylenebilir.
Karışımın, ürün veri sayfasında belirtildiği gibi önerilen indüksiyon süresi boyunca beklemesine izin verilmesi gerekir.
Sonuç
İki bileşenli bir malzemenin üretici tarafından belirtilen orandan farklı bir oranda karıştırılmasının etkileri geniş bir arıza yelpazesine neden olabilir. Bu kusurların bazıları ise kaplama başarısızlığı olarak sonuçlanabilir. Kusurlar, karıştırılan malzemelerin türüne, doğru orandan sapmanın derecesine, karıştırma sırasında çevresel koşullara ve alt tabaka malzemesinin herhangi bir etkisine dayanır. Bileşenlerin oran dışı karıştırılması şüphesi varsa, sahadaki kaplamayı değerlendirmek için kullanılabilen tarama testlerinin yanı sıra, iki bileşenin oran dışı karışımının daha kesin kanıtlarını temin edebilen laboratuvar testleri de mevcuttur.
Referanslar 1. KTA University, Çok Bileşenli Kaplamaların Yanlış Karıştırılması, Erişim Tarihi: 5 Mart 2018, https://ktauniversity. com/incorrect-multi-component-coatings/ 2. http://www.dacrylate.co.uk/Hub/2pckx.html
Seda Ömercikoğlu Yüce, MICorr, PCS
NACE Kıdemli Korozyon Teknolojisi Uzmanı
Genel Müdür
STM Coatech