Epoksi reçineler, epoksit grupları içeren reaktif prepolimer ve polimer malzemelerin genel adıdır. Poliepoksit olarak da bilinen ve 1934 yılında Almanya’da Paul Schlank (1) tarafından sentezlenen ancak bugün bilinen şekliyle ilk kez 1936 da Dr. Pierre Castan (2) ve Dr. Sylwan Owen Grrenlee (3) tarafından üretilen epoksi reçineler, 1950’li yılların başından itibaren endüstrinin birçok alanında yaygın kullanım alanları bulmuştur.
poksi reçinelerin çok farklı uygulama alanları bulunmakla birlikte 2020 yılı itibarıyla 10,5 milyar Dolara ulaşan epoksi reçine pazarının (4) yaklaşık %23 oranındaki bölümü Boya & Kaplama endüstrilerini içermektedir. (5)
•Yapıştırıcılar,
• Kompozit malzemeler,
• Marin,
•Rüzgâr tribünleri/enerji,
• Elektronik,
• Sanat,
• Mobilya,
• Biyomedikal sistemler,
• Havacılık ve uzay teknolojisi
Bazı epoksi reçine uygulamaları Şekil 1’de ve teknik özellikleri Tablo 1’de gösterilmiştir.
[caption id="attachment_126717" align="aligncenter" width="622"]
Şekil 1. Farklı Epoksi Uygulamaları[/caption]
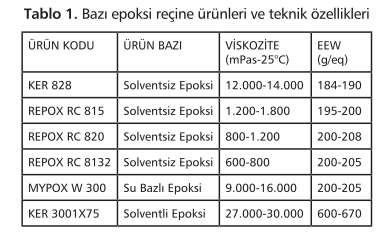
En yaygın epoksi reçineler, epiklorohidrin (ECH) ve bisfenol-A (BPA) arasındaki iki aşamalı bir reaksiyondan üretilen sistemlerdir. Özel reçineler üretmek için farklı formülasyonlar da geliştirilmiştir. ECH ve BPA reaksiyon şeması Şekil 2’de gösterilmektedir.
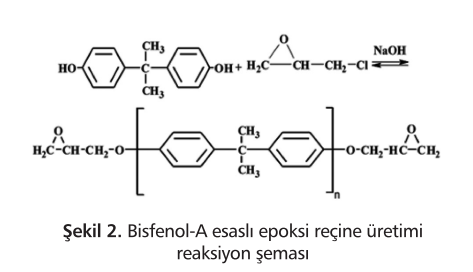
Genel olarak, epoksiler mükemmel yapışma, kimyasal ve ısı direnci, güçlü mekanik özellikleri ve elektriksel yalıtım özellikleri ile bilinirler. Epoksi reçine sistemlerinin güçlü mekanik özellikleri sağlayabilmesi, lineer yapıdaki epoksi reçinelerin üç boyutlu çapraz bağlı termoset yapılar oluşturabilmesine bağlıdır.
Bu işlem ise küratör veya sertleştirici olarak adlandırılan malzemeler kullanılarak gerçekleştirilen kürlenme reaksiyonu ile mümkün olmaktadır (6). Epoksi reçineler için yaygın olarak kullanılan sertleştiricilerin temel baz grupları arasında aminler, asitler, asit anhidritler, fenoller, alkoller ve tiyoller bulunur. Oda sıcaklığında kürlenmesi ve ürünün fiziksel özelliklerinin geliştirilmesine olanak vermesi bakımından özellikle boya ve kaplama alanında amin bazlı sertleştiriciler tercih edilmektedir.
1. Farklı Uygulamalara Göre Sertleştirici Seçimi
Epoksi uygulamaları oldukça geniş bir çeşitlilik içermektedir. Zemin kaplama uygulamalarında astar ve üst kat sistemlerinin yanı sıra, uygulama alanı ve ihtiyaçlara göre belirlenen farklı çalışmalardan bazı örnekler aşağıdaki gibi sıralanabilir.
•Self leveling,
• Portakal kabuğu görünümü,
• Epoksi harç,
• Epoksi boya,
• Anti-korozyon epoksi astar,
•Epoksi seramik yapıştırıcısı,
• Epoksi yapıştırıcı,
• Epoksi derz dolgu.
Uygulamalara göre kullanılacak epoksi reçine ve sertleştirici seçimleri farklı olacağı gibi kullanılması gereken katkı maddeleri ve dolgu malzemesi de sistemin ihtiyaçlarına göre belirlenmelidir. Astar uygulamalarında kullanılan sertleştiriciler renk hassasiyetinin olmadığı durumlarda, endüstriyel kaplamalar ve astarlarda, epoksi harçlarda, yüksek dolgulu sistemlerde ve yüksek kimyasal direnç gerektiren uygulamalarda kullanıma uygundur.
İşleme geçmeden önce uygulama yapılacak alanının zemin etüdü yapılmalı, yüzeyin temiz olduğundan emin olunmalıdır. Yüzeyde gözenekler varsa tamir harcı ile doldurulmalıdır. Tüm zemin hazırlıkları tamamlandıktan sonra epoksi astar kat ile yüzey boyanır. İkinci işlem için astar katın tamamen kuruması beklenir. Bazı durumlarda ara kat yapılabilir.
Yapılan epoksi astar kat işlemi tamamen kuruduktan sonra son kat işlemi uygulanabilir. Bu işlemde çoğunlukla renklendirme tercih edilmektedir. Karışım şeffaf ise ve farklı bir renge sahip olmak istenirse hazırlanan sisteme pigment pasta eklenerek renklendirme yapılır. Son kat işlemi de bitirildikten sonra uygulamanın tamamen kuruması beklenir. Kuruma süresi ile ilgili bilgi, ürünlerimizin teknik özelliklerini paylaştığımız Tablo 2’de verilmiştir. Yapılacak olan zemin ve sistem türüne göre epoksi kuruma süresi farklılık gösterebilmektedir.
2. Sertleştirici Baz Grubu Etkisi
Farklı sertleştirici gruplarının kullanılması nihai ürünün özelliklerinde etkilidir. Ürünün kimyasal dayanımı, parlaklığı, renk stabilitesi de kullanılacak baz gruplarının etkinliğine bağlı olarak değişiklik göstermektedir. Amin bazlı sertleştirici gruplarında seçilen baz aminin ürünün özelliklerine etkisi şematik olarak belirlenmiş ve Şekil 3’te sunulmuştur.
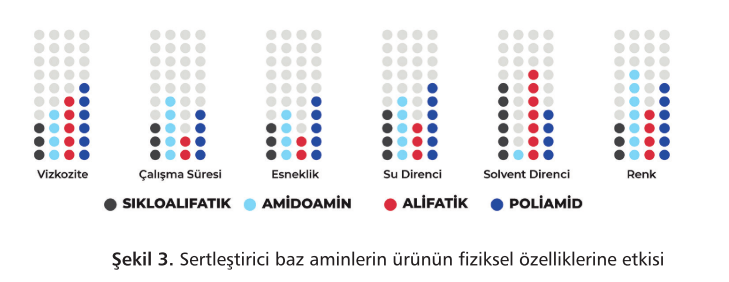
Şekil 3’te görüleceği gibi alifatik amin bazlı sertleştiriciler kullanılarak kürlenmiş reçineler alkalilere, bazı inorganik asitlere ve solventlere karşı iyi bir dirence sahiptirler. Düşük sıcaklıkta kürlenme sağlanır ve pot life oldukça düşüktür. Özellikle solvent direnci gerektiren uygulamalarda alifatik amin bazlı sertleştiriciler kullanılabilir. Öte yandan sikloalifatik amin bazlı sertleştiriciler ise ürünün renk stabilitesi ve parlaklığının önemli olduğu durumlarda gereklidir. Alifatik amin bazlı ürünlere göre daha düşük viskoziteye sahip olması çalışma kolaylığı sağlarken öte yandan kimyasal ve mekanik dayanım açısından da geniş bir ürün yelpazesi oluşturulmasına da katkı sağlayabilmektedir.
Su direncinin önem kazandığı astar uygulamalarında ve nem bariyerli ürünlerde ise poliamid bazlı sertleştiriciler tercih edilmektedir. Bunun yanı sıra mükemmel bir yapıştırma da elde edilebilmektedir. Ancak Pot life süresinin uzun olduğu ve film oluşumundan tam kürlenmeye geçiş süreçleri göz önünde bulundurulmalıdır. Amidoamin bazlı sertleştiricilerde ise yapıştırma özelliği güçlü ürünler elde edilebilir. Kimyasal dayanımın ve su direncinin beklendiği durumlarda tercih edilmelidir.
Farklı baz amin gruplarına sahip sertleştiricilerin uygulama alanları ise Şekil 4’te verilmiştir.
3. Sıcaklık
Epoksi Kürlenme reaksiyonlarında kürlenme hızı sıcaklık ile doğru orantılıdır. Amin bazlı sertleştiricilerin kullanıldığı sistemlerde genellikle kürlenme için oda sıcaklığı yeterli olmakla birlikte kürlenme reaksiyonunun ekzotermik bir reaksiyon olduğu ve jelleşme tamamlanıncaya kadar geçen süre içinde ısı açığa çıkacağı göz önünde bulundurulmalıdır. Belirtilen ekzotermik reaksiyonda açığa çıkan ısı miktarı kullanılan epoksinin miktarına ve uygulama kalınlığına bağlı olarak da artış göstermektedir.
Büyük bir kütlede daha fazla ısı tutulur, bu da daha hızlı reaksiyona ve daha fazla ısıya neden olur. Karıştırma kabının şekli ve karıştırılan miktarın bu ekzotermik reaksiyon üzerinde büyük etkisi vardır. Plastik bir karıştırma kabında bulunan bir kürleme epoksi kütlesi kabı eritmeye yeterli ısı üretebilirken aynı miktar ince bir tabaka halinde yayılırsa ekzotermik ısı dağılır. Uygulanan epoksi tabakası ne kadar ince olursa, ekzotermik ısıdan o kadar az etkilenir ve o kadar yavaş kürleşir.
Sıcaklık azalırsa kürlenmenin tamamlanma süreci uzayacaktır. Daha hızlı kürlenme için ortam sıcaklığının artırılması gerekmektedir. Şekil 5’te epoksi sıcaklığının kürlenme aşamalarına etkisi görülmektedir.
4. Reçine/Sertleştirici Oranı
Epoksi reçine ve sertleştiricinin özellikleri ve miktarı ile reçine/sertleştirici oranı kalitenin ve ürün fonksiyonlarının belirlenmesinde en önemli etken grubunu oluşturmaktadır. Bunun yanı sıra kullanılan dolgu ve diğer katkı maddeleri, ortam sıcaklığı, uygulanan ürünün kalınlığı gibi parametrelerin etkinliği de önem kazanmaktadır.
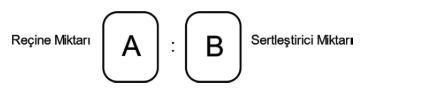
4. Reçine/Sertleştirici Oranı Epoksi reçine ve sertleştiricinin özellikleri ve miktarı ile reçine/sertleştirici oranı kalitenin ve ürün fonksiyonlarının belirlenmesinde en önemli etken grubunu oluşturmaktadır. Bunun yanı sıra kullanılan dolgu ve diğer katkı maddeleri, ortam sıcaklığı, uygulanan ürünün kalınlığı gibi parametrelerin etkinliği de önem kazanmaktadır.
Örnek Hesaplama:
Kullanılacak epoksi reçinenin piyasada çok iyi bilinen, yüksek viskoziteye sahip KER 828 olduğunu varsayalım. A komponenti olarak seçtiğimiz KER 828’in epoksi reçine eş değer ağırlığı (EEW değeri) üretici firma tarafından belirlenmektedir ve TDS dökümlerinde verilmiştir. KER 828 için bu değer (EEW) 188 (g/eq) olarak tanımlanmıştır.
Sertleştirici olarak bu örnekte Recure 503’ü kullanalım. (Bkz. Tablo 2.) Recure 503 AHEW: 115 (g/eq)
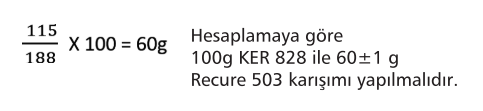
Karışım oranı reçine ve sertleştirici markasına göre değişiklik göstermektedir. Bu sebeple her sistem için muhakkak yeniden hesaplanmalı ve sağlıklı kürleşme için karışımın hesaplanan oran doğrultusunda hazırlanması gerekmektedir. Daha hızlı kuruma için sertleştirici miktarını arttırmak düşünülenin aksine sistemin reaksiyon dengesini bozarak daha esnek kalmasına neden olabilir.
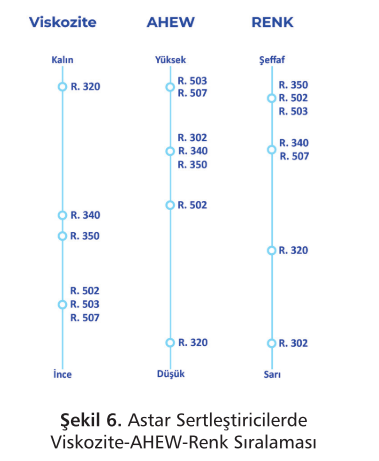
[caption id="attachment_126757" align="aligncenter" width="600"]
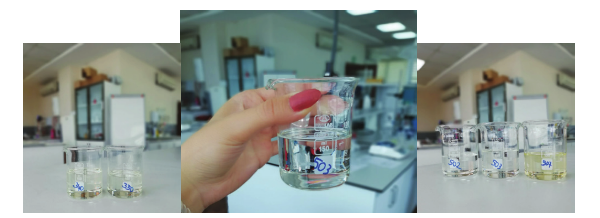
Şekil 7. Bazı sertleştirici gruplarının görünümleri soldan sağa sırasıyla; Recure 340, Recure 350, Recure 503, Recure 502, Recure 503 ve Recure 507.[/caption]
Reaksiyon Kimya A.Ş. 20 yıla yakın süredir inşaat malzemeleri pazarının ihtiyaç duyduğu hammadde tedariği ve üretim faaliyetlerini gerçekleştirmektedir. Epoksi reçine, epoksi sertleştirici, selüloz eter, toz polimer, pigment pasta, wax ve akrilik emülsiyon firmanın üretimini gerçekleştirdiği ana ürün gruplarından bazılarıdır.
Reaksiyon Kimya Anonim Şirketi, Kocaeli Dilovası Organize Sanayi Bölgesi’nde 4500 m² alana kurulmuş olan modern teknoloji ile donatılmış fabrikasında üretim yapmaktadır. Firmanın bütün iş operasyon süreçleri müşteri memnuniyetinin sağlanabilmesi amacıyla tam donanımlı bir AR-GE ve kalite kontrol departmanı tarafından desteklenmektedir. Ar-Ge çalışmalarına verdiği önem ile üretim hacmini büyüterek Türkiye’nin bu sektörde dışa bağımlılığını azaltmak şirketin yegane hedefi olmuştur.
Referanslar 1. P. Schlack, I. G. Farbenindustrie, German Patent 676 117 (1938), US Patent 2 136 928 (1938). 2. US 2444333, Pierre Castan, “Process for the manufacture of thermosetting synthetic resins by the polymerization of alkylene oxide derivatives”, issued 1948-06-29, assigned to DeVoe & Raynolds
3. ^ US 2456408, Sylvan Owen Greenlee, “Synthetic drying compositions”, issued 1948-12-14, assigned to DeVoe & Raynolds 4. TMR, (2015). SpecialChem Coatings and Inks Formulation, (Website: http://www.specialchem4coatings.com) Copyright TMR 5. Epoxy Resins Committee > Socioeconomic Analysis 2013, https://epoxy-europe.eu/wp-content/uploads/2018/11/Epoxy_Socioeconomic_Study_Main_Findings_August-2017.pdf 6. Hakiki, Farizal et al. (2015). Is Epoxy-Based Polymer Suitable for Water Shut-Off Application? SPE-176457-MS. SPE/IATMI Asia Pacific Oil & Gas Conference and Exhibition, 20–22 October, Nusa Dua, Bali, Indonesia. doi: 10.2118/176457-MS