Çelik üretim proseslerinde uygulanan ısıl işlemler sırasında demir, havadaki oksijen ile reaksiyona girmekte ve bu reaksiyon sonucunda çelik yüzeyinde oksit tabakası oluşmaktadır.
Bu oksit tabakası metalin soğuma hızına bağlı olarak FeO, Fe2,O3, Fe3O4 formlarında olabilir. Üretim prosesinin izleyen adımlarındaki yüzey işlemlerinin daha verimli bir şekilde uygulanması için, öncelikle çelik yüzeyinde oluşan oksit tabakasının uzaklaştırılması gerekmektedir. Hidroklorik asit ve sülfürik asit karbon çeliği malzeme yüzeyindeki demir oksit tabakasının giderilmesinde kullanılırken; fosforik asit, nitrik asit ve hidroflorik asit, sülfürik asit ile birlikte paslanmaz çelik malzemenin yüzey temizliği işleminde kullanılmaktadır.
Bu makalede karbon çeliği malzemenin asit ile yüzey temizleme işlemi yanında, işlem sonucu oluşan atık çözeltiden HCl geri kazanımı için yaygın olarak uygulanan yöntemlerden bahsedilecektir.
Yüzey temizleme işleminin başlangıç evresinde havuzlar ağırlıkça %15-22 HCl konsantrasyonuna sahip asit çözeltisi ile doldurulmaktadır. Çelik malzemenin ile asit teması sonucunda, metal oksidin türüne göre başlıca aşağıdaki reaksiyonlar meydana gelmektedir [1].
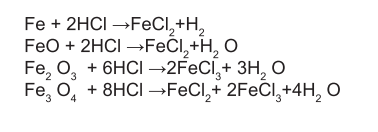
Yüzey temizleme işlemi süresince çözelti içerisindeki HCl konsantrasyonu zaman içerisinde azalırken, demir konsantrasyonu ise artmaktadır. HCl derişimi yaklaşık %5 (w/w), demir konsantrasyonu da 250 g/L FeCl2 (w/v) düzeyine geldiğinde, temizlik işlemi çok yavaşlamakta ve verimsiz hale gelmektedir. Bu durumda havuzlar boşaltılmakta ve yeni asitli çözelti ile doldurulmaktadır. Havuzlardan alınan çözelti ise nötrleştirildikten sonra atık bertaraf tesislerine gönderilmektedir. Bu yöntemin
zayıf yanları aşağıda sıralanmıştır:
• Havuzların boşaltılması için gerekli işçilik, zaman ve üretim kaybı,
• Nötrleştirmek için gerekli kimyasal maliyeti,
• Atık bertaraf maliyeti,
• Çevre dostu bir sistem olmaması [1, 2]
Yukarıdaki dezavantajların tümünü ortadan kaldırmak için sürdürülebilir bir yaklaşım, atık çözeltinin geri kazanılarak sisteme geri beslenmesidir. Bilimsel ve teknolojik literatürde farklı geri kazanım yöntemleri ile ilgili çalışmalar bulunmaktadır. Bu geri kazanım yöntemleriyle yukarıda bahsedilmiş dezavantajlar ortadan kaldırılırken, çözelti içerisindeki HCl ve demir konsantrasyonları etkin bir yüzey temizliği için gerekli düzeylerde tutulup, sürekli ve verimli bir proses elde edilebilmektedir.
Yüzey temizleme işlemi sonucu oluşan atık çözeltiden HCl geri kazanımı için yaygın olarak uygulanan yöntemler aşağıda kısaca incelenmiştir.
1- Pirometalurjik Yöntemler
Pirometalürjik yöntemler atık çözeltinin geri kazanımı için yaygın olarak kullanılan yöntemlerden biridir. Bu yöntemde katı tanecikleri süzülen çözelti, püskürtmeli kavurma ya da akışkan yatak türünde olabilen bir reaktöre beslenip, yüksek sıcaklıktaki yanma gazı ile doğrudan temas ettirilir. Reaktör içerisinde aşağıdaki reaksiyon ile HCl ve demir (III) oksit oluşmaktadır.

Reaksiyon ürünlerinden Fe2O3 sistemden katı olarak alınır. Oluşan HCl ise buhar evresinde olup, su ile çalışan gaz soğurma (absorption) kolonuna beslenir ve sistemden sulu çözeltisi olarak alınır. Bu proses sonucunda elde edilen, asitli çözelti yaklaşık %18 HCl içermekte olup, yüzey temizleme havuzlarına geri beslenir (bkz. Şekil 1).
Bu tepkime püskürtmeli kavurma reaktöründe 350-550 derece sıcaklık aralığında gerçekleştirilirken, akışkan yataklı reaktörde ise 820-880 derece aralığında gerçekleşmektedir. Reaksiyon için gerekli enerji sıcak yanma gazlarından, gerekli oksijen ise yanma gazı ile beslenen fazla havadan elde edilir. [3, 4, 5]
Pirometalurjik yöntemlerle yüksek saflıkta elde edilen Fe2 O3 ticari değeri olan bir yan üründür ve endüstride renk verici malzeme olarak kullanılabilmektedir.
Pirometalurjik yöntemler enerji tüketimi yüksek proseslerdir (600-1200 kcal/L). Aynı zamanda yüksek sıcaklıklarda korozif bir madde ile çalışıldığı için bakım maliyetleri de yüksektir. Yatırım ve işletme maliyeti yüksek olduğundan düşük kapasiteli sistemler için uygun değildir. Yüksek kapasiteli sistemler için daha uygundur [3, 6]
[caption id="attachment_123238" align="aligncenter" width="822"]
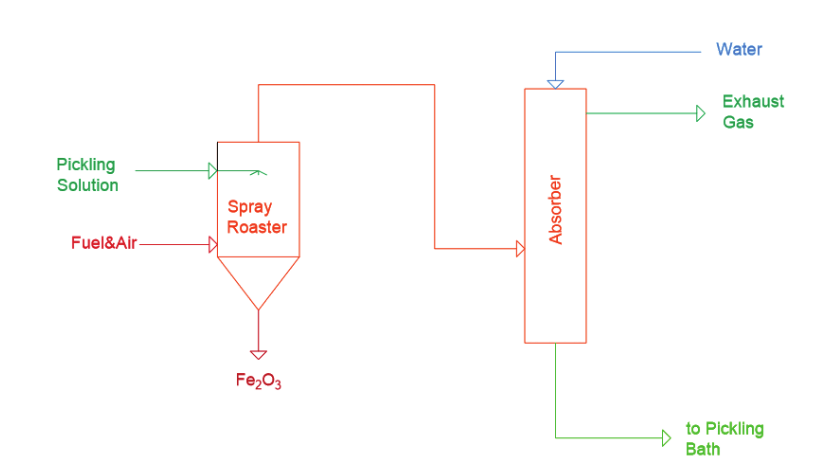
Şekil 1. Püskürtmeli Kavurma Yöntemiyle HCl Geri Kazanımı [3].[/caption]
Bir başka dikkat edilecek yan ise, atık çözeltisi içerisindeki çinko derişimi, 0.5 g/L düzeyinden yüksek olduğunda bu yöntemin uygulanamamasıdır. Bunun başlıca nedeni, yüksek sıcaklıklarda çinkonun reaktör yüzeyine yapışmasıdır. Aynı zamanda reaksiyon sonucu elde edilecek olan yan ürünün saflığı da etkilenmekte ve ürünün ticari değeri düşmektedir. Bu yüzden uygulama öncesinde çözelti içerisindeki çinkonun ayırılması gerekmektedir. Çözelti içerisindeki çinkoyu ayırmak için çözgen ekstraksiyonu yöntemi kullanılabilir. Bu yöntemde birbiri içinde çözünmeyen (su ve yağ gibi) çözelti ve çözgen karıştırılır ve çinko iyonlarının su evresinden, çözgen evresine seçimli aktarımı sağlanır.
Çözgen ekstraksiyonu yönteminde Tribütil Fosfat (TBP) ve CYANEX 302 kimyasalları etken madde olarak kullanılabilir. Çinko iyonlarından ayrılmış asit çözeltisi geri kazanım prosesine beslenir. İkinci aşama olarak çözgen içerikli çözelti su ile karıştırılır ve çinko iyonlarının suya aktarımı sağlanır. Çinko içerikli çözelti galvaniz prosesinde kullanılabilir. Çinko iyonlarından ayrılmış çözgen ise tekrar ekstraksiyon prosesinde kullanılır. Çözgenin geri kazanımı sürecin ekonomisini belirleyen tamamlayıcı adımdır [7, 8, 9].
2. Evaporasyon
Evaporasyon yönteminde, havuzlardan alınan atık çözelti süzüldükten sonra evaporatöre beslenir. Evaporatörün üst akımından HCl-H2O buhar karışımı alınırken, alt akımından ise konsantre FeCl2 çözeltisi alınmaktadır. Daha büyük miktarda sıvı buharlaştırılması durumunda FeCl2O kristalleri de elde edilebilir.
Evaporatörden çıkan buhar damıtma yoluyla zenginleştirme kolonuna beslenir ve burada HCl ve H2O ayırımı gerçekleştirilir. Proses sonucunda %18 (w/w) konsantrasyona kadar HCl çözeltisi elde edilebilmektedir. Kolondan çıkan su buharı yoğuşturulup sistemden alınır ve tekrar kullanılması amacıyla yüzey işlem prosesine geri gönderilir (bkz. Şekil 2) [2].
Pirometalürjik yöntemlerle karşılaştırıldığında evaporasyon yönteminin işletme maliyetleri yaklaşık olarak %50 oranında daha düşüktür [4]
[caption id="attachment_123240" align="aligncenter" width="985"]
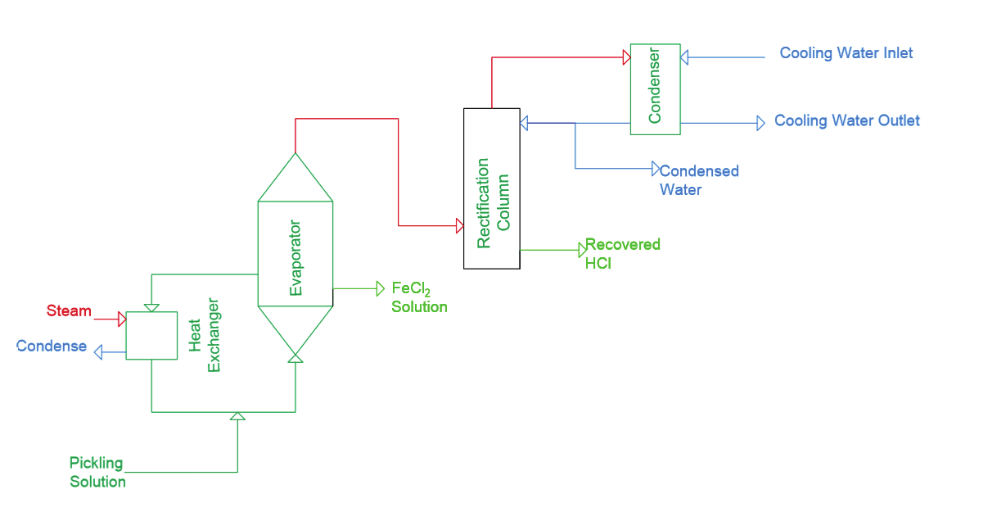
Şekil 2. Evaporasyon Yöntemiyle HCl Geri Kazanımı [2][/caption]
3. İyon Değiş tokuşu
Bu yöntemde anyon değiştirici reçine ile doldurulmuş kolondan geçirilen çözelti içerisindeki HCl reçine tarafından tutulurken, çözelti içerisindeki FeCl2
ve su sistemden alınır. Daha sonrasında kolon su ile yıkanarak reçinede tutulmuş HCl geri kazanılır [10].
Literatürde bulunan çalışmalarda görülmüştür ki bu yöntemle atık çözelti içerisindeki asidin yaklaşık %8090’ı geri kazanılırken, FeCl2’nin de %45-60’ı atık çözelti
içerisinden alınabilmektedir. Asit geri kazanım oranı yüksek olmasına karşın, elde edilen asit konsantrasyonu yaklaşık %8 HCl içerdiğinden diğer yöntemlere göre daha düşüktür. Aynı zamanda FeCl2’nin %45-60 oranında çözeltiden ayrılması da diğer yöntemlere göre oldukça düşük bir orandır [4, 10].
4. Difüzyon Diyalizi
Difüzyon diyalizi yönteminde seçici geçirgen bir membran kullanılmaktadır. Şekil 3’te görüldüğü gibi membranın bir tarafından çözelti beslenirken, diğer tarafından deiyonize su beslenir. Membranın iki tarafındaki çözeltiler içerisindeki asit konsantrasyonları farkından dolayı, asit seçici geçirgen membrandan deiyonize su tarafına aktarılır. Membranın bir tarafından asidi uzaklaştırılmış metal içerikli çözelti çıkarken, diğer tarafından HCl içerikli çözelti alınmaktadır.
Proses sonucunda asit geri kazanımı %80-90 düzeyinde sağlanırken, FeCl2 geri kazanımı %75 düzeyinde sağlanabilmektedir. HCl çözeltisi yaklaşık %6 düzeyinde elde edilmektedir. Bu derişim diğer yöntemlere göre düşük bir düzeydedir [4, 11].
[caption id="attachment_123241" align="aligncenter" width="988"]
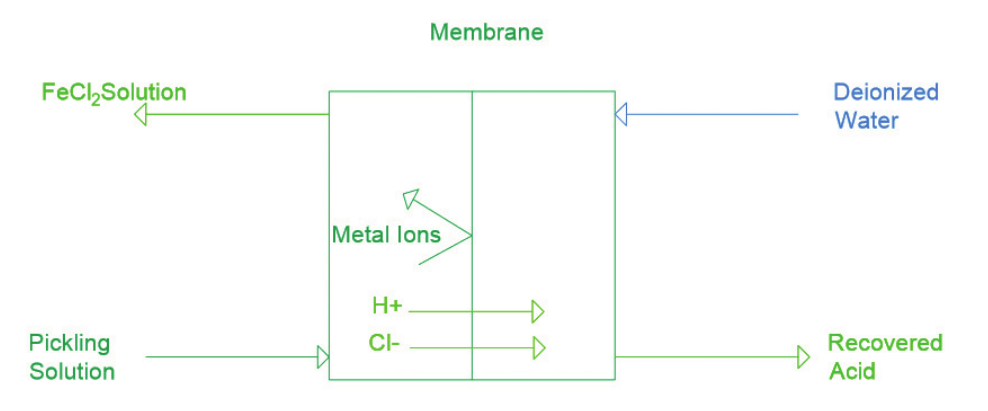
Şekil 3. Difüzyon Diyalizi Yöntemiyle HCl Geri Kazanımı [11][/caption]
5- Atık Çözeltiden Demir Sülfat Heptahidrat Elde Edilmesi ve Hidroklorik Asit Geri Kazanımı
Bu yöntemde atık çözelti içerisine sülfürik asit eklenerek aşağıdaki reaksiyon yoluyla demir (II) sülfat ve hidroklorik asit meydana gelmektedir.
FeCl2 +H2 SO4 →FeSO4 +2HCl
Reaksiyon sonucu elde edilen çözelti soğutulup, kristallendirilerek ticari değeri olan FeSO4.7H2O yan ürünü elde edilir (bkz. Şekil 4).
Reaksiyon sonucunda ağırlıkça %30 HCl çözeltisi elde edilir. Bu yöntemle atık çözelti içerisindeki demirin %90’ı demir sülfat olarak kazanılabilmektedir [7, 12, 13].
[caption id="attachment_123242" align="aligncenter" width="767"]
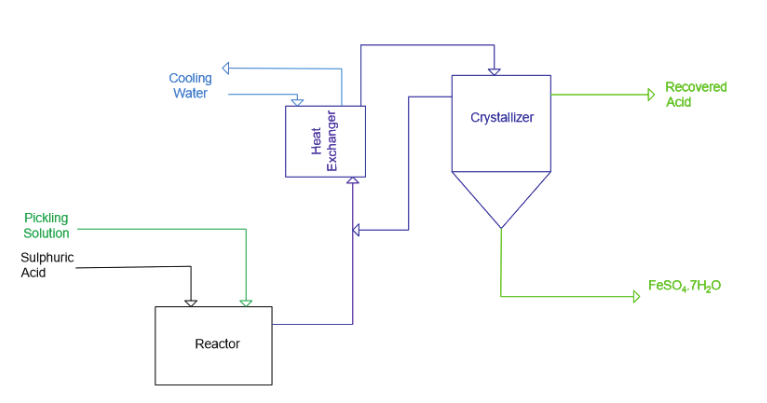
Şekil 4. Atık Çözeltiden Demir Sülfat Heptahidrat Elde Edilmesi ve Hidroklorik Asit Geri Kazanımı [7, 13] . [/caption]
Bilimsel ve teknolojik kapsamda yapılan araştırmalarda metal yüzey işlemleri sonucunda oluşan atık asit çözeltisinin geri kazanımı ile ilgili pek çok çalışmaya rastlanmıştır. İşletmelerin yaygın olarak kullandığı yöntemlerin başında pirometalurjik yöntemler gelmektedir. Bununla birlikte pirometalurjik yöntemlerin yatırım ve işletme maliyeti, diğer sistemlere kıyasla daha yüksek olduğu için, düşük kapasiteli sistemlerde yatırımın geri dönüş süresi uzun olmakta ve bu yüzden de düşük kapasiteli sistemlerde uygulanamamaktadır. İyon değiştokuşu ve membran ile ayırma yöntemlerinde diğer yöntemlere kıyasla daha yüksek miktarda FeCl2 içerikli ürün alınmaktadır. FeCl2 yan ürünü her ne kadar ticari değere sahip bir ürün olsa da, ticari olarak daha yaygın kullanım alanı olan FeCl3'e dönüştürülebilmesi sisteme daha fazla katma değer katacaktır.
Atık çözelti içerisinden demir iyonlarının uzaklaştırılması açısından bakıldığında iyon değiştokuş ve membran ile ayırma yöntemleri, diğer yöntemlere göre daha düşük verimde ayrım sağlamaktadır. Yukarıda bahsedildiği gibi geri kazanılan çözeltide demir oranının düşük olması yüzey temizleme işleminin verimliliğini etkilemektedir.
Referanslar
[1] Liu, Y., Wang, L., Liu, L., Han, W., Sun, X., Li, J., and Shen, J., Hydrochloric acid pickling process optimization in metal wire working, International Journal of Simulation: Systems, Vol. 16 (5), pp. 1.1-1.6. [2] Kantaşlı, Ş., ‘Atık yüzey temizleme çözeltilerinden asit geri kazanımı’, http://www.turkchem.net/atik-yuzey-temizleme-cozeltilerinden-asit-geri-kazanimi.html, Accessed December 29, 2020.
[3] Rosocka, M. R., 2010, A review on methods of regeneration of spent pickling solutions from steel processing, Journal of Hazardous Materials, Vol. 177, pp. 57-69.
[4] Cullivan, B., Cullivan, J., 2016, Economic and chemical comparisons of hydrochloric acid recovery technologies for iron pickling operations.
[5] Baerhold, F., Mitterecker, S., 2016, Acid recovery in the steel and metallurgical industry process characteristics and fuel saving options, 4th
International Symposium on Iron Control in Hydrometallurgy.
[6] Devi, A., Singhal., A., Gupta, R., and Panzade, P., 2014, A study on treatment methods of spent pickling liquor generated by pickling process of steel, Clean Technologies and Environmental Policy, Vol. 16, pp. 1515–1527. [7] Tusset, S., 2017, ‘Hydrochloric acid recovery and liquid waste treatment from exhausted pickling baths’, https://blog-en.condorchem.com/, Accessed December 29, 2020. [8] Grzyeszczyk, A., Rosocka, M. R., 2007, Extraction of Zinc (II), Iron (II) and Iron (III) from chloride media with dibutylphosphonate, Hydrometallurgy, Vol. 86 (1-2), pp. 72-79.
[9] Regel, M., Sastre and A. M., Szymanowski, 2001, Recovery of Zinc (II) from HCl spent pickling solutions by solvent extraction, Environmental Science & Technology, Vol. 35 (3), pp. 630-635.
[10] Brown, C. J., (1990), “Productivity Improvements Through Recovery of Pickle Liquors with APU Process”, Iron & Steel Engineer, Vol. 67, January, pp. 55-60.
[11] Gueccia, R., Aguirre, A. R., Randazzo, S., Cipollina, A., and Micale, G., 2020, Diffusion dialysis for separation of hydrochloric acid, iron and zinc ions from highly concentrated pickling solutions, Membranes, Vol 10 (6). [12] Kumar, M. S., Ghare, N. Y., Vaidya, A. N., and Bal, A. S., 1998, Recovery of acid from pickling liquors, Enviromental Engineering Science, Vol. 15 (4), pp. 259-263.
[13] ‘Acid Recovery Technology’, www.komalchemiequip.co, Accessed December 29, 2020.
Nurcan Demirçivi
Kimya Mühendisi
Sistemas