Fast Sample Dryers, Bucket Test System and Further
One of the problems is encountered in the production of paints is the long drying times of the coating samples which come from the production for the color measurement. The drying times of solvent-based coatings may take hours and curing of powder coatings takes approximately 10-15 minutes.
Another problem is the determining whether the packages have enough mechanical strength or not before filling. Here we will discuss about the new equipments and techniques which are developed in order to solve these problems.
Long drying times of the paint and similar coating materials can cause to increase downtime of manufacturing process, stoppage of manufacturing machines and unproductiveness of workers.
In order to speed up this process, eMEDa designed emok for solventbased coatings and etok for powder coatings. emok reduces drying times of coating samples from hours to minutes without deteriorating their chroma, hue and gloss properties.
This equipment has three radiation sources. The temperature of the film should be controlled during the drying, for the solvent evaporation heat transfer or reaction energy should be transmitted to the material by radiation.
The wavelength and intensity, also duration and interval of radiation are important in order to find the fastest program. For example, water-based products are rapidly affected by microwaves.
When microwave is applied with suitable wavelength, angle, filters and intervals; it can separate the water from the film in seconds almost like a molecular sieve. But such a fast program can deteriorate the film.
Therefore microwave should be combined with other radiation sources and power of these sources should be adjusted properly. Moreover, rotary table should pass the samples through the sources in order to dry samples evenly.
emok is precisely designed and developed in order to fulfil the optimum conditions for fast drying of paint samples. It can dry some industrial paints in 20 minutes. Luxury and enamel style coatings can be dried in 8 minutes and water based coatings can be dried in 2-3 minutes.
Water-based coatings which are high-textured can be dried in 6-7 minutes, and plasters which are few millimeters can be dried in 10-12 minutes.
Thanks to its user friendly software, drying times can be optimized for the product and product groups easily and thereafter drying process can be made independently from the laboratory assistant.
10 to 60 watts of energy required for drying a film and approximately 2400 watts of energy should be absorbed and vented out as a harmless hot air. This process is especially necessary for the microwave.
In addition, harmful gases that may occur during drying should be vented out with a separate flue. It is important point to take into account in order to ensure occupational health and safety.
emok is a novel equipment and standards have not been set for this kind of devices yet. Due to its multiple radiation sources it can be used as a weathering device as well as fast dryer.
There are no comparable results yet but test methods can be created similar to the standard tests of weathering devices and it can provide faster test opportunities.
For example; the UV strength of a new type pigment or resin / binder can be accurately tested in a few hours. It can provide preliminary information before long-term weathering tests which take days or months.
Essentially, emok are produced in order to decreases downtime of production but it can be useful in research, product development and improvement projects. It also can be can used in food, ceramics and other chemistry areas.
The most common problem in packaging is unwanted costs of strengthless buckets. They usually stacked on top of each other and lowest buckets should carry the load constantly. They also need to be durable against the heat, cold and impacts.
If strength of lowest bucket is not enough lid or plastic wall of bucket can break. Also strength of handle is important. Other packaging problem examples are; dust collection of buckets because of electrostatic effect, breaking when dropping and leaking from the lid.
Now packing manufacturers have begun to test their products in order to improve their quality level and decrease rejection rate of non-conforming products. Manufacturers usually test their products when they change the design or formulas of raw materials.
Also some packaging users take few buckets and test them before deciding to accept or reject the goods. The companies which are packaging users may need more such tests because they tend to demand different packages from different suppliers.
ekta, is designed specially to test the packagings and perform strength tests by applying controlled force upon the materials. At reasonable speeds (ex. 5 mm/s), the maximum load that a plastic package with a volume of 20 liters can withstand is 750 kg.
A plastic container of about 3 liters can resist a maximum load of 300 kg. Metal packagings of similar volume can be 20-50% more resistant than plastic. Handles can withstand loads up to 30 kg in 3 lt containers and up to 65 kg in 20 lt plastic packagings at similar speeds.
While the metal handles have a resistance of over 100 kg, the plastic handles which have been made recently are resistant to over 80 kg. The speed of use force for the test is 5 mm/s which is similar to virtual speed (holding the bucket by a person or impacts during transportation).
In the plastics industry, material testing speeds may vary, but since standards are not developed in these tests each organization has to set its own criteria, such as in weathering tests. Such tests need to be perceived as technical quality control tests, not scientific studies of R&D.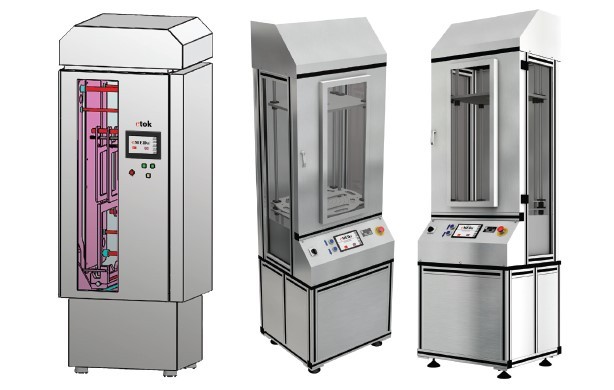
While the air pressure is a method applying force in the application, it is almost impossible to adjust the speed and the repeatability of the results is low since the air is a compressible fluid. Pressure fluctuations in the air lines of the plant may adversely affect the repeatability.
An electrically operated mechanism provides more reliable results and operate stable. Thanks to its servo motors, ekta has speed and ramp identification possibilities. Therefore the test can be performed independently from the laborant. Conventional tension and compression devices and their apparatus are highly expensive.
So ekta which is specially designed for this test and much more cost effective can be preferred. As bucket is used in food industries for packaging, it can be useful in this industry. Also a stack strength test in a cardboard package or routine strength tests of different adhesives with a suitable apparatus can be made with ekta.
Our customers who benefited from the advantages of emok decreasing the drying times of wet paints, stated that a device which shorten also drying times of powder coatings could be beneficial for themselves. In line with this demand coming from our customers, we designed this device named etok.
Infrared and ultraviolet sources are used for etok like our other device emok and also induction technology is benefited. etok can shorten the curing time from 10-15 minutes to 3-5 minutes by decreasing 300%.
This shortens the production process and reduces the costs by allowing to test the samples rapidly during powder coating production. Also, it can be useful in research, product development and improvement projects. Furthermore, our device can be useful for the other sectors except from powder coating manufacturers.
For the above mentioned innovative devices, numerous test have been made and models have been developed for many years. In the new model of ekta which we designed especially for bucket tests, we make studies in order to add the measurability of resistance against the dust collection, that’s the anti-static status of plastic material.
Also we continue our studies in order to reveal the advantages of detecting correlations among standard weathering test devices’ results with emok fast film dryer which have multiple, programmable resources. Finally, all products of eMEDa provide a safe use in compliance with CE directives.
Hasan Hüseyin Engin
Chemical Engineer, M. Sc.
Owner and Director
eMEDa