SprayVision, It is not What You Look at That Matters, It is What You See
SprayVision would like to introduce you to technology for spray pattern analysis, its evaluation and wet thickness measurement.
This technology was developed based on a need from the coating industry to understand better the output of spray guns and rotary bells and to be able to analyze them with the possibility to optimize the output. This technology can be used with any kind of paint and can be very easily installed with any sort of spray painting system.
SprayVision is composed of hardware which captures spray patterns applied on transparent foils or tapes (Figure 1) and software (Figure 2) which evaluates them.
How does SprayVision work?
The first step is to spray a pattern (Figure 3-4) or coat the product. It is then possible to evaluate static patterns, dynamic patterns and tapes of different shapes which can be applied before coating directly on the part surface (Figure 5-6).
With tapes applied on the part an analysis of the trajectory connections and a full description of thickness distribution can be known. The second step after paint application is to put the foil or tape into the SprayCapture hardware.
Please note that it is actually possible to do this in the wet stage without drying of the paint first. Thicknesses, volumes and other outputs are recalculated on dry values with deviation lower than 5%. (Figure 7). All of this is possible without waiting and passing through the whole spray line process.
Due to the spray pattern or tape being captured, you are able to start with the analysis and evaluation immediately. The most important functions are described and shown in the picture below (Figure 8).
,
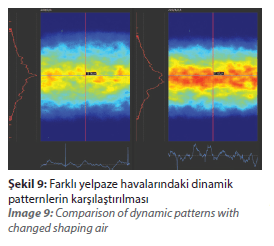
1. Captured Pattern Input received from SprayCapture
2. Evaluation With Basic Size Dimensions of pattern Calculation of applied volume Evaluation of transfer efficiency Distribution of paint Cross section in „X“ and „Y“ axis
3. 3D Model Of Pattern Better understanding of effective part Visualisation of paint distribution with „Z“ value Useful for further analysis
4. Pattern Comparison Comparison of patterns and its volume Identification of pattern with higher transfer efficiency
5. Application set up Shows spraying parameters set for shown pattern
SprayCapture – Basic analysis of patter and its first evaluation included thickness, volume, 3D model and cross sections of pattern.
Patterns comparison 2D/3D
Dynamic patterns are very important for evaluation of transfer and understanding of paths connection during robot programming. SprayVision allows you to evaluate SB 50 (metrics of path distances) from dynamic pattern and calculate the transferred volume.
Based on this information it is possible to say which parameters to use for spraying – those with highest transfer and good atomization. This could then be verified directly on the part by using our tapes. Figure 9 shows a dynamic spray pattern for interior car plastic parts where just shape air was changed from 3 bar to 2.5 bar.
Here you can see that the volume increased significantly. You can spray many patterns and based on the transfer decide which is best for your purpose. This will reduce the amount of paint you use and save on costs.
Process control
Provides you with a tool for an objective assessment of patterns. Once you identify your required spray pattern for your project it is important to check before actual production and after changing the air cap, or just occasionally if the spray output is still as you require.
The pattern is sprayed and then inserted in SprayCapture. Within minutes the operator will receive an objective evaluation of shape, volume, width and height match. If there are any anomalies in the process, you will be able to see these and based on these results identify the actual problem which should be corrected.
- Comparison of production pattern against standard pattern.
- Fully automatic comparison and output for operator.
- Independent comparison of size, shape and volume.
- Identification of defect with warning option.
Paths connection
Allows you to control the connection of coating trajectories and uniformity of paint layer. When using more spray guns or air caps you can easily compare them and understand each individual spray output. In Figure 10 at next page, it is possible to see the output of each individual spray gun from a horizontal line.
The set-up on the main control panel was completely the same, however, the actual output of the spray gun was significantly different. When comparing robot applications where two robots are mirrored differences are often found, which should then be corrected.
Figure 11 shows the tape which was applied on the bumper in Figure 6 and the graph shows how the thickness is wavering.
Thickness measurement
Obtain thickness values which will be on a surface before it becomes dry from a wet film. You do not need to wait for hours – especially when new projects are waiting to be implemented.
The procedure is as follows: the part is sprayed with spot or surface tape on it: In flash- off insert tape into SprayCapture and then the captured thickness values are shown. You will always get the precise measurement values even if the viscosity or solid content changes.
Offline programming
This allows you to create a very realistic program without wasting parts or spray booth time. You can process everything without actual drying of the wet stage. Firstly, it is important to find the correct parameters with the highest transfer, actual required size and
good atomization. Once set, it is then possible to design the dynamic spray pattern. With the dynamic spray test it is immediately known what the thickness will be on the main surfaces of the parts. This will save hours of spray line and waiting time.
In addition to this any additional tuning on the actual parts and problematic areas should be carried out. However, a significant part of the programming will have already been done. By using SprayVision you will get an innovative and effective technology that ensures unbeatable quality, productivity and financial savings.
Kemalcan Süzen - Teknik Satış Yöneticisi - Technical Sales Executive - Latro
•
Financial
- Identification of transfer efficiency,
- Optimization of spraying parameters.
- Process control ,
- Reduction of scrap.
•
Productivity
- Increasing of transfer,
- Greater process control.
•
Quality
- Verification of production standard,
- Accurate understanding of spraying output,
- Immediate identification of spraying defects.
•
Environment
- Reduction in paint used,
- Reduction of VOC.
•
General
- Fast reaction to any kind of defect,
- Database with filtering and production overview,
- Installation close to spray line.