2K Water-Borne Polyurethane Systems without Sacrificing Drying Time
By Dr. Eva Tejada, Covestro SL, and Dr. Hans-Josef Laas and Dr. Berta Vega Sánchez, Covestro Deutschland AG. Around 40% of the global industrial wood coatings market is based on traditional solvent-borne polyurethane technology.
Water-borne polyurethane systems are high performance and environmentally compatible, but their inherently slower drying has limited the market shift towards this low emission alternative. A novel hybrid hydrophilic polyisocyanate offers a fast-drying and promising solution.
The industrial wood coatings market, which represents 5% of the global industrial coatings market [1], is still dominated by 2K solvent-borne (SB) polyurethane technology [2], due to the combination of:
• High mechanical and chemical resistance,
• A unique balance of flexibility and hardness,
• Very fast drying, which enables high productivity.
Sustainability is becoming more important and this comes with the increasing need for alternatives to reduce VOCs in coating applications.
Water-borne (WB) based solutions are already available on the market, but users need to choose between systems with fast drying but low performance (1K polyacrylate (PAC) systems) or high-performing systems with slower drying (2K WB PU).
Unlike in other applications, SB wood coatings often rely upon aromatic or mixed aromatic/aliphatic polyisocyanate crosslinkers to accelerate drying.
Yellowing caused by aromatic polyisocyanates is not a problem for clear coatings on wood, as the wood itself has a high tendency to yellow (to an even greater extent than the yellowing caused by the aromatic polyisocyanates).
For white pigmented systems, aliphatic polyisocyanates (or blends with aromatic polyisocyanates) are used in combination with polyols to achieve low yellowing levels, if required, but this comes at the expense of slower drying.
Hardener is Key to Developing Fast Crosslinkers
On the contrary, aliphatic hydrophobically modified water- emulsifiable polyisocyanates [3] are used to formulate aqueous two-component polyurethane coatings.
Modern WB 2K PU coatings are certainly comparable and sometimes even superior to solvent-borne coating materials with respect to mechanical and chemical resistance.
However, their noticeably slower drying behaviour prevents further penetration in the wood sector as the finished parts cannot be sanded or stacked until dry.
By choosing aqueous fast-drying polyols, the reactivity of the 2K WB systems can be improved, but it has not yet been possible to match the fast drying of 2K SB PU coatings.
It is the hardener that determines the curing speed of the system and it is therefore the hardener that needs improvement to achieve the difficult milestone of developing fast crosslinkers that work in water-based coatings.
Novel HDI-TDI Hardener for Faster Curing of 2K WB Systems
By choosing the right monomers and optimising the amount and type of hydrophilization, we could develop the first mixed aliphatic-aromatic polyisocyanate based on HDI and TDI, which is suitable as a crosslinker component for 2K WB PU coating systems.
The use of this new crosslinker in combination with available standard aqueous binders leads to significantly faster drying compared with established water-emulsifiable polyisocyanates.
This novel hardener; Bayhydur® quix 306-70, (Table 1) allows the formulation of fast-curing WB 2K PU wood coatings of polyurethane quality, with high mechanical and chemical resistance, good film appearance, and long pot life.
Faster Cure with Minimal Compromise
The novel hardener has been tested in different systems to study the benefits of the novel HDI/TDI trimers. Properties have been compared by preparing coatings based on two different hardeners (novel PIC versus a standard HDI trimer anionically hydrophilized (STD PIC)) combined with two different acrylic polyols: a primary (Prim. PAC) and a secondary (Sec. PAC). The primary PAC is a 40% solid content acrylic dispersion with 1.5% OH based on solid, whereas the secondary PAC contains 40% solid contents and 3% OH based on solid. We used the same NCO/OH for comparison.
Comparable gloss and haze values are obtained in the final films when exchanging the standard hardener by the novel one (see Figure 1). As expected, coatings containing the novel hybrid hardener cure significantly faster than those prepared using the standard aliphatic polyisocyanate.
There is a clear improvement in T4 (total drying) which is linked to the reactivity of the hardeners. The sand drying time is virtually unaffected by the aromatic character of the hardener, as T1 relates to the solvent and water evaporation and not to the reactivity of the crosslinker (Figure 2).
The faster curing is also noticeable in the faster hardness evolution of the system when the novel PIC is being used (Figure 3).
Despite the faster curing shown in the examples above, the formulations based on the novel PIC have a long enough pot life (the tested formulations achieved >7 hours). Depending on the formulation, we observed some reduction in the pot life, but in general there is no need to sacrifice pot life.
As the novel polyisocyanate is based on anionic hydrophilization, the coating achieves very high chemical resistance even in white pigmented coatings. The chemical resistance of a coating based on aliphatic/aromatic polyisocyanate (novel PIC) is comparable to the obtained with a standard high-end hydrophilic polyisocyanate (STD PIC): the system based on the novel hardener is able to pass DIN 68861-1B, meaning it is able to pass even the 16h coffee and 6h red wine test even in a white pigmented formulation.
The new hardener was also tested in combination with a polyurethane polyol dispersion (OH-PUD). This polyurethane dispersion is 38% solid and contains 3% OH. This polyurethane is characterised by very high final hardness and being very fast drying [4].
Figure 4 shows the drying and hardness evolution of this polyurethane polyol, combined with the two types of polyisocyanates. Even in such a fast system, it is still possible to reduce the curing time by up to 60% using the new HDI/TDI hydrophilic hardener.
A further advantage of the new product is that it is easier to down-gloss for matt formulations. It is well known that faster systems require less matting agent, thus the faster curing of the novel PIC saves matting agent. As an example the OH-PUD formulation needs 20% less TS100 to get same gloss values (1.8% used with STD PIC to get a gloss at 60°C of 18 GU vs 1.4% in the case of the novel-PIC to get a gloss at 60°C of 15 GU).
Drying Time Comparable to 2K SB Standard
In general, by optimising the ratio of aromatic content in the hardener and combining with the right polyol, a water-borne system can achieve comparable reactivity to standard 2K SB PU systems at significantly lower VOC levels and yellowing behaviour.
Table 2 compares two standard solvent-borne aromatic systems with two formulations based on the new hardener. The solvent-borne systems are based on a polyester polyol cross-linked with aromatic polyisocyanates and are compared with two 2K WB coatings based on the new hardener.
We chose two different polyols for the water-borne formulations; a primary acrylic polyol and an OH-functional polyurethane dispersion.
The table shows that the water-borne coatings based on the new hardener can match or even improve the standard solvent-borne systems, but at a much lower VOC level. The use of the polyurethane polyol reduces the VOC level even further, as this product can be formulated without adding a co-solvent.
An additional benefit is that the product’s yellowing behaviour is closer to an aliphatic product, despite the specific aromatic character of the new hydrophilic hardener (see Figure 5), which means the system is also suitable for white pigmented formulations.
More environmentally friendly solutions now possible A new hydrophilic HDI/TDI polyisocyanate crosslinker allows the formulation of high performance 2K WB PU coatings with similar reactivity as standard solventborne 2K PU systems, but with much lower VOC levels and improved yellowing behaviour.
All other coatings properties are at the same level as the current high-performance standard, 2K WB systems. This new development will facilitate the shift from the well-established 2K solventborne technology towards more environmentally friendly high-performing water-borne solutions.
Results at A Glance
• Solvent-borne polyurethane technology currently dominates the wood coating market due to its high performance and rapid drying,
• A novel hybrid hydrophilic polyisocyanate offers a more environmentally friendly alternative,
• The new aromatic-aliphatic crosslinker makes it possible to formulate high-performance 2K water-borne coatings that dry as fast as standard solventborne systems but with lower VOC.
• The yellowing behaviour is close to that of an aliphatic product, which means the system is also suitable for white pigmented formulations.
Figure 2. Drying time comparison at room temperature (23°C, 50% RH) of different 2K WB coatings (based on secondary and primary acrylic polyol and two different hardeners) according to DIN 53150, 120 g/m2 on glass. Total dry (T4) of 2K WB systems can be reduced by half compared to a standard system when using the novel hardener
Figure 3. Hardness evolution of coatings based on different polyols combined with both hardeners. New development shows faster hardness evolution than homologue HDI type.
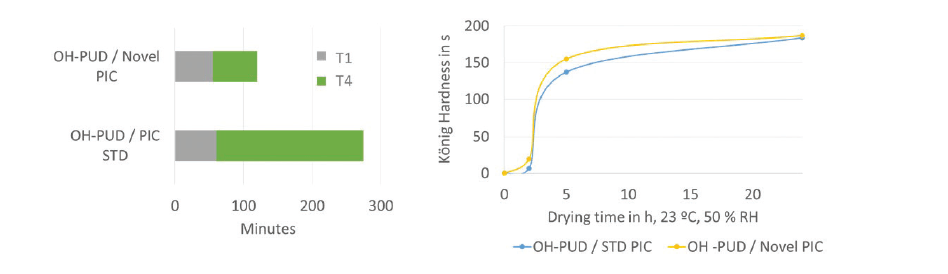
Figure 4. Drying and hardness evolution of coatings based on OH-functional PUD and different hardeners. The novel PIC shows faster hardness evolution than homologue HDI type
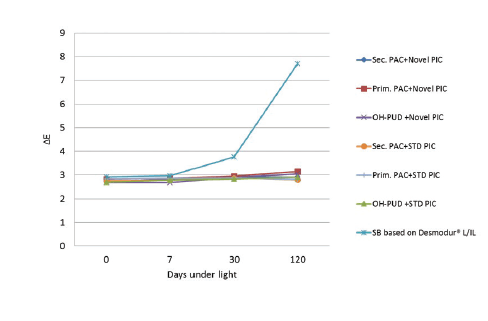
Figure 5. Comparison of yellowing under natural light (under glass 45ºC oriented south) from coatings based on new hardener and standard types (aliphatic and aromatic)
References
[1]O. Menukhin, Irfab-Marktstudien, Polyurethanlacke, FARBE UND LACK, 04/2018, S. 15
[2]IrfabTM Global Industrial Coatings Markets (GICM), PRA World Ltd (2017)
[3]Meier-Westhues U., Danielmeier K., Kruppa P., Squiller E. P., Polyurethanes: Coatings, Adhesives and Sealants,
2nd Revised Edition Hanover: Vincentz Network 2019, p. 48 - 51
[4]Maria Almatö, Martin Melchiors, Eva Tejada “The solventless solution” European Coatings Journal 07 | 08 l
2010, p.38