Ship owners endeavor to create jobs that grow profitably. Each decision is calculated to bring higher profits to the business. An important decision of the owners of marine chemicals and product tankers is to select the coating of the cargo tank or the tank material with the highest return on investment (YKG).
The focus of this article is to present economies that make this important decision. I will present it from the perspective of the ship owners and operators. Because they can get the highest YKG from their tanks in this way..
There are a wide variety of liquid chemical cargoes transported in marine tankers and they are defined in three categories:
• Organic Chemicals made from hydrocarbons such as oil and natural gas and used to produce other chemicals, plastics and resins. This group represents approximately 60% of the liquid chemicals market and includes important cargoes such as Methanol, MTBE, Xylene, Styrene, Benzene, Toluene and others.
,• Inorganic Chemicals, which are mainly composed of acids, make up another 15% of the liquid transport market.
• Vegetable oils and animal fats, such as palm oil and soybean oil, which are used as raw materials for various industrial processes and complement the remaining 25% of the transport market.
Each chemical cargo is classified according to its transport requirements as defined in the UKK Coding (International Bulk Chemical Code), which imposes strict regulations on the design of the ship, onboard equipment and handling procedures.
IMO (International Maritime Organization) assigns a class for each cargo based on toxicity rate, flammable capacity, abrasiveness and reactivity. Thus, the transport of a particular chemical makes it necessary to check whether the cargo carried by the shipowner corresponds to the tanker’s capabilities.
Now, as a ship owner, how do you maximize the sales potential of your fleet? Obviously you can do this by transporting the most profitable and high specification cargoes wherever possible, and accepting the cargoes offered by optimizing the cargo volume of the ship.
This includes being able to transport organic chemicals and vegetable oils / animal fats that make up 85% of the liquid transport market.
Maximizing cargo tanks at any one time has a tremendous financial advantage. Therefore, as a ship owner, you need to evaluate the various types of cargoes currently being transported and plan the improvement of existing vessels and / or purchase of newly built ships to transport higher specification cargoes that provide more profit and / or provide more diversity.
Then decide which type of tank material or primer / coating will work for your needs. The option is to build tanks with phenolic epoxy or a high performance MarineLine® polymer-based primer / coating or a conventional protective coating such as stainless steel.
Which approach provides the highest LAG? The following economic analysis reviews the performance capability, tank construction, application, inspection, as well as ongoing operational and cleaning issues.
A stainless steel tank has a passivated surface that resists corrosion and rustiness and therefore can carry a variety of chemicals.
This is estimated at approximately 24% of IMO-rated chemical tankers of 1,000dwt and above, and stainless steel tanks have been used since 1999. Stainless steel has a good performas history. However, it comes with a high entry point for the newly constructed construction and its ongoing maintenance is expensive.
The performance of a stainless steel tank is dramatically reduced when exposed to halogen salts and especially chlorides that penetrate passivation and allow corrosive attack.
Because chlorides are one of the most common elements present in nature, they create ideal conditions for corrosion and chemical attack and require extensive repair and maintenance.
In order to tackle this problem, more shipowners specify duplex stainless steel tanks, which are even more expensive but offer higher levels of corrosion resistance.
It is estimated that conventional epoxy and phenolic epoxy coatings represent approximately 59% of the chemical tanker market. They are used for a variety of services, including certain organic acids, alcohols, edible fats,animal fats and solvents. However, these coatings are not suitable for all corrosive liquids.
Most manufacturers state that no aggressive cargo will be loaded in the first three months.At the same time, after transporting an aggressive cargo, an approved non-aggressive cargo should be transported to avoid any coating problems.
Attempts to carry out cargo operations in such a way and with difficulty take the cost of occupation in profitable cargo sequencing, compromise diversity and ultimately reduce potential profits.
Another option for shipowners is to specify MarineLine® 784 from Advanced Polymer Coatings (Avon, Ohio, USA). MarineLine® has become a popular choice for ship owners due to its high chemical resistance, variety and ease of cleaning.
Since its introduction about ten years ago, it has acquired approximately 12% of the primer / coating tank market.
MarineLine® 784 is formulated with a unique polymer using 28 functional groups per molecule. When fully cured, MarineLine® 784 coating forms a 3-dimensional sieve-like and almost impermeable structure up to 784 cross-linking, compared to the minimal crosslinking of an epoxy using only 2 functional groups for 4 cross-links per molecule only. It is easy to understand that a more permeable surface with less cross-linking allows for easy chemical attack and cargo absorption.
The main gains of ship owners using MarineLine® are the ability to transport a wide variety of aggressive cargoes and CPPs, PFADs, Bio-Fuels, Methanol, Ethanol and others, and then to easily replace cargoes.
MarineLine® is also generally recognized as safe (GRAS) for food grade cargoes, and corresponds to United States F.D.A. regulations and all food regulations in force.
Now, compare the estimated costs of manufacturing stainless or carbon steel tanks, as well as tank primers/coatings, inspection and heat curing. It is estimated that the stainless steel tank construction typically costs about three times as much as a carbon steel tank coating coated with phenolic epoxy or MarineLine®.
Stainless steel tanks can be as durable as the life of the ship. However, ongoing passivation adds more to maintenance costs.
The organic priming/coating ages over time and aging can be accelerated by aggressive cleaning for quick return and cargo cycle.
Thus, primed/coated tanks sometimes need to be repaired and/or recoated, resulting in downtime. MarineLine®-coated tanks offer long service life and lower maintenance costs compared to stainless steel.
With proper maintenance, MarineLine® tanks provide many profitable years. Since the initial cost is only one-third of stainless steel, YKG is achieved faster, and the greater diversity of MarineLine® phenolic epoxy coatings allows more cargo to be transported than tanks.
MarineLine®’s small Priming/Coating repair work can be performed by a ship’s crew using the APC MarineMend Kit, a user friendly repair system and procedure used when a small portion of the primer/coating is damaged.
Larger repairs or coating of the tank is carried out while the ship is connected outside of duty, where appropriate application conditions and heat curing are provided and monitored.
When a ship is put into service, a minimal waiting time is essential to put the ship into profitable operation after unloading at the port. Ship owners require the shortest ventilation recovery time and the fastest possible return with the minimum cleaning chemicals needed to pass Wall wash washing tests.
In this way, the lining / coating material of the tank provides the best addition for YKG. With stainless steel, cleaning of the tank can be costly due to problems within itself arising from chloride attack.
Typical cleaning to remove residues of cargo is first carried out with sea water at a certain temperature, followed by cleaning with fresh water and cleaning to remove chlorites.
For some cargos, only fresh water is used. After that, it is necessary to passivate at various points throughout the life cycle of the cargo tank in order to maintain a quality stainless steel tank. Passivation depends on the cargoes being transported.
After certain final cargo restrictions, shipowners can disable stainless steel tanks to comply with FOSFA’s latest cargo requirements. It is estimated that 16 percent of the maintenance budget of an entire stainless steel tanker is allocated for maintenance over the lifetime of the ship, which is a high cost.
Phenolic epoxy coatings have very high absorption properties, especially with a product such as Methanol, and have high levels of restrictions on cleaning and cargo loading. In addition, there are severe cargo restrictions on the transport of oils and other sensitive cargoes used as human food.
Also, after handling aggressive watersoluble cargoes, no vapor, ballast water, wash water or aqueous cargoes should come into contact with the phenolic epoxy coating before the coating condition is restored by ventilation.
All these “extra” cleaning requirements and shipping limitations of stainless steel and zinc and epoxy coatings result in lost revenue.
Marine - Line’s hard, slippery and ultra-smooth surface is easily cleaned with commonly used chemicals and eliminates long aeration times while substantially eliminating the risk of subsequent cargo contamination and allowing the ship to be serviced more quickly.
Independent laboratory tests show that MarineLine is equal to, even if it is not better in terms of cleanliness and chemical resistance, stainless steel and other coatings.
MarineLine® requires forced ventilation 24 hours after completion of transport of methanol in the tanks, and cargo tanks are not allowed to evaporate after the discharge of Methanol. In laboratory surface topography tests that measure surface roughness,
MarineLine® (Ra from 0.7 to 0.9) and Phenolic Epoxies (Ra from 1.8 to 2.1) and Stainless Steel (Ra from 3.2 to 4.5) are considered to be less slippery, when the lower number is considered more slippery.
What distinguishes MarineLine® from other coatings is that it is ready to load all cargoes on the MarineLine® durability list upon delivery from the shipyard.
Other coatings must wait a period of time for natural cure to load any particular non-aggressive cargo, and with certain aggressive cargoes, the waiting time may extend up to three months for service and hot curing, and epoxy coatings may still have limitations. We can determine this situation numerically with AHP (Analytic Hierarchy Process) method.
13. Elongation (%) (according to ASTM D 522) KPI13
14. Surface energy ( dynes/cm)( according to ASTM D 2794) KPI14
15. Surface roughness (according to ASTM) KPI15
16. Recoating & repair cost (within 20 years)(usd/sm2) KPI16
17. Recoating or repair time (year) KP17
18. Warranty KP18
B. Main coating types in chemical tankers:
1. 316L type Stainless Steel cargo tank
2. Marineline 784 type cargo tank
3. Phenolic epoxy type cargo tank
C. Functionality of KPIs
Table 1
According to three different coating types with 14000 dwts capacity 12 cargo tanks and 2 slop tanks of a chemical tanker 14000. According to 18 KPI types :
Conclusion
In order to select the most suitable coating method in chemical tankers, AHP and Normalization method were used.
Accordingly, a total of 18 criteria (KPI) were determined and criterion values were entered in the 3 most common types of coating used in today’s chemical tankers. The evaluation was based on a chemical tanker with 12 cargo tanks + 2 slop tanks with a capacity of 14,000 dwts.
Accordingly, in a chemical tanker with 14,000 dwt capacity, 12 cargo tanks and 2 slop tanks we applied, according to the Analytic Hierarchy Process method, after 8 steps, among the 3 most common types used nowadays (stainless steel, marineline coating, phenolic epoxy coating) coating. numerically, the best method is “Marineline Coating was determined to be the best method numerically.
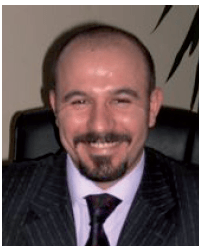
Capt. Koray Karagöz
General Manager
Marineline Türkiye
References
[1] ASTM Standards.
[2] IBC List of Chemicals.
[3] Dr.verwey labs,reported date 26.07.2015 cert.no10556435.
[4] MarinSpec Associates,Report Date October 2009.
[5] APC’s report Coating Application&DH Comprasion date 19 february 2015.
[6] “Tank kaplamalarının önemi” -Turkchem Nisan-Mayıs 2011.
[7] “Tank kaplamaları kullanmak için kararı Ekonomi verdirir. ” Endüstriyel boyalar & Toz boyalar ve Teknolojileri dergisi.
[8] Wacker Chemie AG.
[9] VAE Copolymer Dispersions, K.Merlo, PCI magazine March 2011.
[10] BOSAD Bülten No :1,2008.
[11] CEPE,AB VOC Ürün direktif sunumu, Dr.J. Warnon İstanbul,2008.
[12] EU Counsil,Directive 2004/42/EC.
[13] EU Counsil,Directive 1999/13/EC.
[14] Indoor Air 2008,August 2008, Paper ID : 953.